Repair or Replace? – Material Tensile Strength Key to Repairability
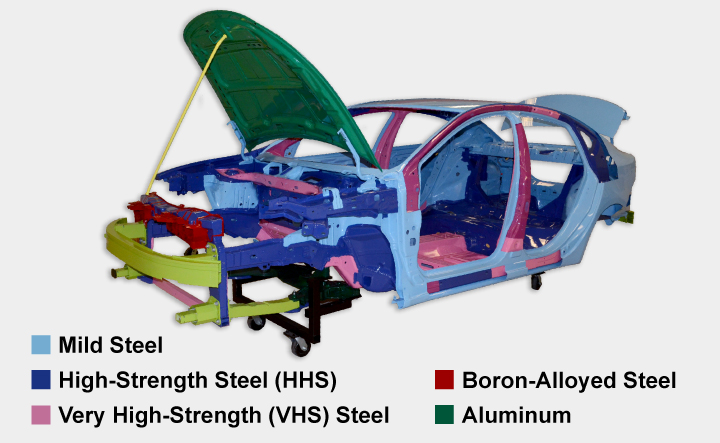
Repair or Replace? – Material Tensile Strength Key to Repairability
Jason Bartanen, I-CAR Director, Industry Technical Relations
The world of steels continues to evolve at a rapid pace and repair professionals need to keep up. In order to perform complete, safe, and quality repairs, it’s imperative to identify the type of material we’re working with, to know what is repairable, and know which options we have for part replacement when straightening is not an option.
20 Years in the Making
In recent years, auto manufacturers have been tasked with reducing vehicle weight, while making vehicles safer (added weight) and still providing all of the entertainment (added weight) and information systems (added weight) that today’s consumers demand. These opposing forces have required auto manufacturers to modify their approach to vehicle construction. For the past two decades, most of the modified approaches have been linked to different types of steels. For many years, the majority of vehicles were constructed of mainly mild steel, with some high‑strength steel (HSS) used on occasion, and ultra‑high‑strength steel (UHSS) used for a number of door intrusion beams and bumper reinforcements. But that started to change, 20 years ago.
(In broad terms, mild steels typically fall in the range up to 210 MPa; HSS between 210–600 MPa; and UHSS, anything above 600 MPa. (1 MPa is equal to 145 psi; therefore, 600 MPa would equal 87,020 psi). These numbers do vary from OEM to OEM, but generally speaking, these are common ranges.)
In 1994, a number of steel manufacturers (35, to be exact) started on a mission to “demonstrate a lightweight steel auto body structure that would meet a wide range of safety and performance targets.” The result of that collaborative effort was the UltraLight Steel Auto Body (ULSAB) vehicle – a vehicle structure that weighed up‑to 36% less than a vehicle of similar size, but constructed with common (at the time) types of steel. This work led to many of the Advanced High‑Strength Steels (AHSS) found on today’s vehicles.
The ULSAB was built using more than 90% HSS and UHSS, and was the dawn of the automotive industry hearing terms such as:
- Dual‑phase (DP)
- Transformation Inducted Plasticity (TRIP)
- Complex Phase (CP)
- Boron
- Hot Stamped and Hot Formed
- Martensitic
- Hydroforming
- Tailored blanks
- Laser welding
While these terms are more widely known today, their meanings aren’t always clear, and often add an additional layer of complexity to “repair vs. replace” decisions taking place, on a daily basis, in collision repair facilities nationwide.
What is important to know, from a repairability standpoint, isn’t necessarily the type of steel (DP, TRIP, CP, etc.), or manufacturing process (tailored blanks, hydroforming, and hot-stamping), but the tensile strength of the material (DP600, DP800, DP1000, etc.). The tensile strength of the materials is what enables collision repair professionals to determine if a part can be straightened, or if it requires replacement; and if it requires replacement, it often dictates the attachment method(s) allowable (sometimes, required) to repair today’s late‑model vehicles.
AHSS Repairability
Just because a part is made of AHSS, doesn’t necessarily mean it can’t be straightened. Some vehicle makers offer repairability guidelines, based on the type and tensile strength of the steel. While lower‑tensile‑strength steels tend to offer more opportunities for straightening, some automakers allow cold straightening up to 700 Megapascals (MPa). OEMs including GM, Ford, Chrysler, Toyota, and Honda provide guidelines on the types of materials that can be straightened, and whether or not heat can be used for straightening. High‑strength steels are more prone to losing strength than mild steel when heat is used for straightening. Ultra‑high‑strength steels are extremely heat sensitive and will lose their strength if heat is applied, for straightening. Always follow the vehicle maker’s guidelines for the use of heat.
A guideline that has historically been used to make repair vs. replacement decision is the I‑CAR® Kink vs. Bend Rule. Simply stated, bent parts were often repairable and kinked parts required replacement. The former definition of a kink was “a sharp bend with a small radius over a short distance. A part is considered kinked if, after straightening, there is a permanent area of deformation, which will not return to its original state and shape without the use of excessive heat. Kinked parts may also have visible cracks or tears in the metal.” It’s important to restore both the shape and the state of the part. If either of these is incomplete, following straightening, the part should be considered kinked and should be replaced.
The kink vs. bend rule is no longer as simple as it sounds. A part may not look like it is kinked, but it may not be able to be straightened without damaging the grain structure, if it isn’t already damaged by the collision. The damage may be in the form of micro-cracking which is not easy to see. In more extreme cases, cracking may occur during straightening which is easier to see, and will require part replacement.
The stronger the steel, the less repairable it becomes. For example, attempting to straighten a slight bend in a UHSS part may cause it to crack, if it is able to be straightened at all. When steel in the 600–800 MPa range must be straightened, as a best practice, a dye penetrant should be used to ensure no micro-cracking has occurred in the steel. Some vehicle makers do not recommend straightening UHSS parts that are above 600 MPa due to the potential of cracking and tearing the part, and the possible damage structural pulling can do to adjacent panels and other parts of the vehicle structure.
If the part is bent, but the thickness or strength of the metal will not allow for straightening without leaving an area of permanent deformation, then replacement, either partial or complete, would be appropriate.
Identification
Because repairability is often dependent on the type of steel used, it’s critical to know the strength of a part when making repair decisions. There are a number of options that can be used to identify the strength of steel found in today’s vehicles.
The first, and most reliable, is referring to the vehicle maker’s body repair manual. Many OEMs are doing a great job of clearly identifying the construction materials used in their vehicles. This information, coupled with OEM repairability guidelines, is the most effective way to determine what can be repaired and what requires replacement.
Another dependable way to identify the strength of a part is to use strength identification equipment. The GYSTEEL VISION is one tool that can be used to identify steel strength. After cleaning the steel (two‑sided access is required), the VISION is attached to the steel part and tightened in place. A measuring pen is then used to take a reading of the steel. The number on the pen is compared to a chart provided by the tool maker to identify the strength of the steel.
Another option, although significantly less reliable than the aforementioned options, would be to attempt to identify the steel, based on its location on the vehicle. All vehicles are built with the consideration of collision energy management. The front, and rear of the vehicle is designed to collapse in a collision, and the center section, around the passenger compartment, is designed remain intact, protecting the occupants, so it transfers the collision energy rather than absorbing it, as collapse zones of the vehicle do. Using this “logic,” it is reasonable to believe that those steels found in the front and rear may have less strength than those on the side of the vehicle; especially reinforcements in the A‑ and B‑pillars, rocker panels, and roof rails.
However, this logic isn’t always accurate, as General Motors is now employing 700 MPa material in the front, lower rails on some of their vehicles – for example, the Cadillac ATS. Considering that the design trend is for steels to become increasingly thinner to save weight, they will need to become stronger as well. Because of that, if any assumption is made as to an unknown type of steel used on a side structure of a vehicle being repaired, it should be that the parts are UHSS. The outer panels may be relatively softer steels to allow easier forming, but even outer panel strengths are increasing as panel thickness is being reduced for weight savings.
Partial Part Replacement
If a part requires replacement, it does not always require complete replacement. A number of vehicle makers allow for partial replacement at factory seams, or for sectioning those parts.
Partial replacement of an assembly at factory seems is an approach that vehicle makers, such as Honda, have taken. For example, the lower rail on a late‑model Accord is serviced as a complete assembly, including a portion of the rail that attaches under the passenger compartment. If the damage is confined to an area forward of the cowl, Honda allows that assembly to be dismantled, just forward of the cowl, and installed. This creates a less intrusive repair, by allowing OEM spot welds, under the passenger compartment, to remain intact and leaves OEM corrosion protection undisturbed. Not all vehicle makers allow this type of procedure, so it’s important, as always, to refer to the vehicle maker procedures. If there are no recommendations from the vehicle maker for, or against, this type of procedure, collision professionals must carefully weigh the advantages before making the decision to move forward with this type of repair.
Other vehicle makers offer a variety of sectioning procedures for many of their structural parts. Unlike partial replacement of an assembly at a factory seam, sectioning allows the technician to replace a portion of a part by marking and cutting the part at a vehicle maker identified sectioning location. Some vehicle makers offer multiple locations, within a single part, for sectioning; others offer only one location. Sectioning should only be done in locations identified by the vehicle maker. The joint configuration of the sectioning location should also be determined, based on the vehicle maker procedures.
In the late 1980s, I‑CAR developed general sectioning guidelines that were used by industry professionals for many years. These general sectioning guidelines are no longer applicable on late model vehicles. For a complete recap of those general sectioning guidelines, visit the I‑CAR Repairability Technical Support (RTS) portal. The article can be found at: Update: Are General Sectioning Guidelines Still Applicable?
In the next I‑CAR article, we’ll take a closer look at the attachment methods for installing parts
Rapid Changes Requires Rethinking
We are in the midst of a “technical tsunami” with the rapid advancements in vehicles, including the world of steels. Repair professionals need to keep up to date with the latest changes in technology, materials, processes and training. The old way of repairing or replacing is not necessarily the right way to perform complete, safe and quality repairs of today’s complex vehicles. It is crucial to accurately identify the vehicle material and determine what is repairable versus replaceable, and to know your options.
The I-CAR Welding Training & Certification program includes instruction on welding theory, a hands-on evaluation by the Instructor of the facility’s gear, equipment, and infrastructure prior to the in-shop training, practice, and the industry-recognized certification test. More information on all of I-CAR’s welding courses (steel GMA welding, aluminum GMA (MIG) welding, and Steel sectioning) can be found at www.i-car.com. As part of I-CAR’s commitment to the industry, pricing for welding training has been reduced to make it more affordable for every technician to have the hands-on training needed to complete a proper weld.
A growing number of OEMs use I-CAR Welding Training & Certification in their network programs, including Acura, Audi, Chrysler, Ford, GM, Honda, Infiniti, Jaguar, Land Rover, Lexus, Nissan, Porsche, Scion, Toyota, Volvo and Volkswagen. In addition, businesses that achieve Gold Class, the industry standard for collision repair training, also include welding training as a program requirement.
Whether it’s steel, aluminum, other vehicle construction materials, or a combination of materials, it’s important that you equip your facility with the proper tools, equipment, and training to allow for complete, safe, and quality repairs. These investments can lead to increased profitability, improved operational efficiency and productivity, and higher customer satisfaction and retention levels.
Jason Bartanen is the I-CAR Director of Industry Technical Relations and is responsible for the I-CAR Repairability Technical Support initiative, at the I-CAR Tech Center in Appleton, WI. He has over 25 in the collision repair industry, the last 18 with I-CAR. Prior to his current role, Bartanen served several roles at I-CAR; as an Instructional Designer, Technical Development Manager and most recently as the Technical Director. Bartanen also assists in managing I-CAR’s specialty training development and delivery programs for a number of vehicle manufactures. Bartanen is a member of the SkillsUSA Collision Repair Technology committee.
*Used with the permission of Fixed Ops Magazine
Additional I-CAR Collision Repair News you may find helpful:
Related I-CAR Courses
-
Toyota/Lexus/Scion Position Statement: Pre- and Post-Repair System Scanning
Thursday, 28 July 2016
As the industry continues to ask if pre- and post-repair system scanning is necessary, Toyota/Lexus/Scion provides their answer.
-
Pre- and Post-Repair System Scanning Statements
Wednesday, 9 January 2019
Are you wondering if a particular OEM or organization has a published statement on pre-repair and post-repair scanning? We have compiled a list of most of the statements on the subject, so you can...
-
ADAS, Calibration, And Scanning Article Hotspot
Monday, 14 January 2019
Since advanced driver assistance systems (ADAS), scanning, and calibration first started becoming relevant, members of the collision repair industry have required as much knowledge as possible on...
-
Honda/Acura Position Statement: Pre- and Post-Repair System Scanning - UPDATE
Wednesday, 22 May 2019
Honda /Acura has updated their position statement on pre- and post-repair scanning to give more clarification on what is expected for scanning.
-
BMW Position Statement: Pre- and Post-Repair System Scanning - UPDATE
Friday, 10 April 2020
BMW has released a position statement related to pre- and post-repair system scanning. The statement applies to All vehicles equipped with on board diagnostics II (OBD II).
-
Quickly Identifying Outer Quarter Panels w/Rolled Hem Flanges
Monday, 5 March 2018
The I-CAR best practice article, Recycled Outer Quarter Panels w/Rolled Hem Flanges has gotten a lot of interest from the collision repair industry. It’s important to know which vehicles are...
-
General Motors Position Statement: Pre- and Post-Repair System Scanning
Friday, 21 October 2016
As the industry continues to ask, are pre- and post-repair scans necessary, General Motors provides their answer.
-
Restraints Wiring Repairs
Monday, 23 May 2016
Over the past few months, we've been sharing OEM position statements on restraints wiring repairs. Now we're bringing them all together in one place for easy reference.
-
FCA/Stellantis Position Statement: Pre- and Post-Repair System Scanning
Thursday, 9 June 2016
FCA/Stellantis has released a position statement related to pre- and post-repair system scanning.
-
Nissan/INFINITI Position Statement: Pre- and Post-Repair System Scanning - UPDATE
Monday, 14 January 2019
Nissan/INFINITI updated their position statement on pre- and post-repair scanning. The revised position statement touches on more subjects and gives additional information on the subject.
-
Repairer Driven News: Rivian Updates Door Handle Procedure
Sunday, 4 February 2035
Repairer Driven News (RDN) released an article featuring an updated Rivian procedure.
-
GM Part Replacement Without A Procedure
Friday, 22 August 2025
We are often asked, “What do I do if there isn’t a procedure to replace a service part?” Let’s see what GM says.
-
App-Based Connected Services Considerations: Ford/Lincoln
Tuesday, 19 August 2025
Have you had the experience where the vehicle notified the owner that it was being moved while it was in your repair facility? App-based connected services are available from many vehicle makers and may...
-
Digital Key Considerations: Ford/Lincoln
Tuesday, 19 August 2025
The intermingling of technology and automobiles continues, with digital key offerings from most vehicle makers. Digital keys utilize smartphone technology to expand vehicle access and owner...
-
Volkswagen Restraints Wiring - UPDATE
Thursday, 14 August 2025
The question is often asked, "Can supplemental restraints system wiring be repaired?" The answer is: it depends on the vehicle maker. Let's take a look at Volkswagen's position on this subject.
-
Jaguar Land Rover Restraints Wiring - UPDATE
Thursday, 14 August 2025
The question is often asked, "Can supplemental restraints system wiring be repaired?" The answer is: it depends on the vehicle maker. Let's take a look at Jaguar Land Rover's position on this subject.
-
I-CAR Repairers Realm: GMA Welding Machine Technology, Setup, And Maintenance - Coming Soon
Wednesday, 13 August 2025
I-CAR is having a discussion on GMA Welding Machine Technology, Setup, And Maintenance.
-
Great Designs In Steel 2025 Presentations: A Closer Look At The VW ID.Buzz Body-In-White Construction
Friday, 8 August 2025
In case you missed it, Eike Schuppert presented the VW ID.Buzz Body-In-White Construction at Great Designs in Steel 2025.
-
Backup Battery And Low-Voltage Disconnect
Wednesday, 6 August 2025
When an accident happens, how will you call for help? Maybe the telematics system, equipped with a backup battery, could automatically do this, even if the main power is cut off. What are the repair...
-
Backup Battery And Low Voltage Disconnect: Kia
Wednesday, 6 August 2025
When an accident happens, how will you call for help? Maybe the telematics system, equipped with a backup battery, could automatically do this, even if the main power is cut off. What are the repair...
- 2025
- August 2025 (10)
- July 2025 (11)
- June 2025 (11)
- May 2025 (11)
- April 2025 (13)
- March 2025 (11)
- February 2025 (11)
- January 2025 (12)
- 2024
- December 2024 (8)
- November 2024 (11)
- October 2024 (13)
- September 2024 (10)
- August 2024 (12)
- July 2024 (11)
- June 2024 (9)
- May 2024 (13)
- April 2024 (12)
- March 2024 (12)
- February 2024 (12)
- January 2024 (10)
- 2023
- December 2023 (8)
- November 2023 (12)
- October 2023 (11)
- September 2023 (11)
- August 2023 (12)
- July 2023 (9)
- June 2023 (11)
- May 2023 (12)
- April 2023 (11)
- March 2023 (12)
- February 2023 (10)
- January 2023 (11)
- 2022
- December 2022 (11)
- November 2022 (12)
- October 2022 (11)
- September 2022 (13)
- August 2022 (11)
- July 2022 (10)
- June 2022 (13)
- May 2022 (11)
- April 2022 (12)
- March 2022 (10)
- February 2022 (11)
- January 2022 (13)
- 2021
- December 2021 (13)
- November 2021 (11)
- October 2021 (13)
- September 2021 (14)
- August 2021 (12)
- July 2021 (15)
- June 2021 (17)
- May 2021 (14)
- April 2021 (14)
- March 2021 (20)
- February 2021 (14)
- January 2021 (14)
- 2020
- December 2020 (13)
- November 2020 (17)
- October 2020 (12)
- September 2020 (14)
- August 2020 (11)
- July 2020 (18)
- June 2020 (16)
- May 2020 (14)
- April 2020 (20)
- March 2020 (12)
- February 2020 (13)
- January 2020 (14)
- 2019
- December 2019 (13)
- November 2019 (19)
- October 2019 (25)
- September 2019 (20)
- August 2019 (22)
- July 2019 (23)
- June 2019 (20)
- May 2019 (19)
- April 2019 (20)
- March 2019 (20)
- February 2019 (18)
- January 2019 (18)
- 2018
- December 2018 (19)
- November 2018 (19)
- October 2018 (17)
- September 2018 (16)
- August 2018 (21)
- July 2018 (20)
- June 2018 (21)
- May 2018 (17)
- April 2018 (19)
- March 2018 (21)
- February 2018 (15)
- January 2018 (20)
- 2017
- December 2017 (13)
- November 2017 (15)
- October 2017 (19)
- September 2017 (20)
- August 2017 (20)
- July 2017 (18)
- June 2017 (19)
- May 2017 (19)
- April 2017 (13)
- March 2017 (18)
- February 2017 (10)
- January 2017 (11)
- 2016
- December 2016 (9)
- November 2016 (14)
- October 2016 (21)
- September 2016 (10)
- August 2016 (11)
- July 2016 (8)
- June 2016 (10)
- May 2016 (6)
- April 2016 (11)
- March 2016 (12)
- February 2016 (11)
- January 2016 (8)
- 2015
- December 2015 (9)
- November 2015 (7)
- October 2015 (8)
- September 2015 (7)
- August 2015 (11)
- July 2015 (7)
- June 2015 (5)
- May 2015 (7)
- April 2015 (8)
- March 2015 (8)
- February 2015 (9)
- January 2015 (10)
- 2014
- December 2014 (12)
- November 2014 (7)
- October 2014 (11)
- September 2014 (10)
- August 2014 (9)
- July 2014 (12)
- June 2014 (9)
- May 2014 (12)
- April 2014 (9)
- March 2014 (6)
- February 2014 (1)
- January 2014 (26)