It's Not Just About Aluminum
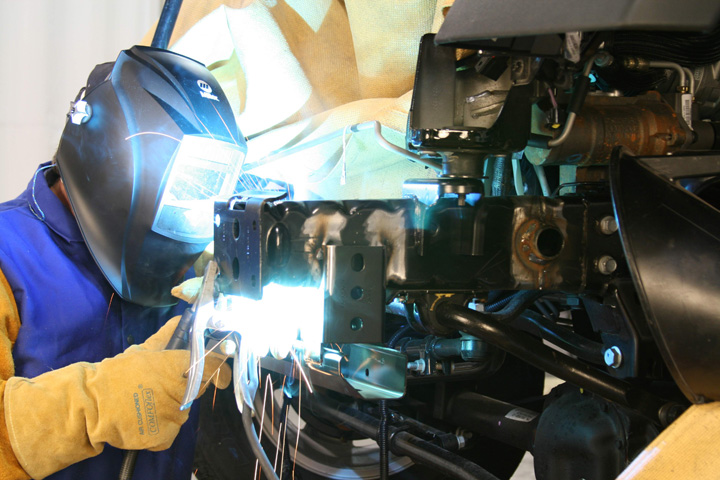
Today's Vehicles Require Updated Collision Repair Tools And Training
by Jason Bartanen
Ever since the unveiling of the 2015 Ford F-150 at the North American International Auto Show in Detroit in January, the U.S. automotive industry has been buzzing about this game changing, aluminum intensive vehicle.
Dealerships and independent collision repair facilities across the country have been trying to determine which new tools, equipment, products and materials will be required to repair this latest generation of one of the best-selling vehicles in the U.S.
While the Ford F-150 and aluminum have been getting most of the press lately, there's a lot more going on in vehicle design and construction of today's vehicles about which repairers should be aware. In addition, taking steps toward equipping their facilities with the necessary tools and the latest training to repair today's vehicles has become critically important.
This investment in tools and training for today's vehicles can actually increase your profitability, improve dealership operational efficiency and productivity, and raise customer satisfaction and retention levels.
Ford F-150 – Designed for Repairability
Following the all-new Ford F-150 announcement, there have been countless articles about clean rooms, rivet guns and aluminum GMA (MIG) welders. Fortunately, Ford has been proactive in developing a comprehensive tool and equipment package, available through Rotunda, for repairers to gear up for the arrival of the new F-150 (currently targeted for a November, 2014 launch).
Ford was also proactive in ensuring that the new F-150 was built with collision repairs in mind. The new vehicle will offer a significant number of collision repair procedures for repair of the unitized cab structure and the high strength steel frame. There are a variety of sectioning options available for the unitized cab structure and the "apron tube" offers a more efficient replacement option. The apron tube on the current model is attached to the cab, through the laminated steel cowl, and requires removal of the instrument panel for replacement. The new, aluminum intensive F-150 offers an apron tube that's attached to the A-pillar from the factory, with rivets and flow drill screws (FDS). The replacement procedure for the apron tube calls for rivets and adhesives and will no longer require removal of the instrument panel.
Although a significant portion of the unitized structure is replaced using rivets and adhesive, there are a number of sectioning procedures available that will allow for aluminum GMA (MIG) welding. For any welding done on the F-150, Ford requires a 220V pulse welder and 1.2 mm 5554 electrode wire.
Ford has also teamed up with the world's leading collision repair training organization, the Inter Industry Conference on Auto Collision Repair (I-CAR®) to develop training for the F-150. I-CAR has been training the Ford dealership network since May and is currently providing the same training to the rest of the industry (independent collision repairers and insurance representatives) and this will continue through the fall. The comprehensive training course will provide insight into the construction of the F-150, provide detailed information on available repair procedures and provide guidance on the necessary tools and equipment that will be required to perform complete, safe and quality repairs for Ford F-150 owners.
It's Not Just About Aluminum
While the requirements for aluminum repair have been widely publicized, the significant changes in steel vehicle construction have gone largely unnoticed by many -- and that's a problem!
"I've been repairing cars for 30 years." "It's just a steel vehicle." These are two of the most common reasons given when it comes to collision repairs on late model steel vehicles. This wouldn't be a problem...if we were repairing 30 year old vehicles. However, today's steel vehicles are changing at a rapid pace. Using repair techniques and equipment from 30 years ago (or even 10 years ago) WILL compromise the structural integrity of today's cars, trucks and SUVs.
Today's consumers shop for 5-star crash-rated vehicles and it's the industry's responsibility to ensure that we're returning their vehicles to pre-accident integrity, following collision repairs. Using improper tools, equipment or techniques limits our ability to do so. How many stars are you compromising by not equipping your facility with the proper tools and equipment?
Let's take a look at welding as an example. Advanced materials have changed the way vehicles should be welded, which makes staying current with welding training critical.
Squeeze-Type Resistance Spot Welding
Over the past several years, squeeze-type resistance spot welding (STRSW) has become the preferred method by many vehicle makers for the replacement of high and ultra high strength steel parts. Some vehicle makers have gone so far as to require STRSW for part replacement.
The current (beginning in 2013) Honda Accord has a handful of reinforcements made of 1,500 MPa steel. The reinforcements cannot be straightened and cannot be sectioned. Honda also requires STRSW for installation for the majority of the parts and warns against GMA (MIG) plug welds: "NEVER perform "MAG" or "MIG" welding on 1,500 MPa steel". (That's a pretty bold statement.) Additionally, there are areas of the vehicle where STRSW isn't possible, due to limited access to both sides of the panel. In these areas, Honda requires MIG brazing. (More on that in a bit.)
Unfortunately, it's not quite as simple as just buying a good quality STRSW machine. Electrical requirements apply to all welders. It's also critical that your facility has the proper electrical requirements installed to ensure your investment performs properly. Too often (and unbeknownst to them) repair facility owners invest in this important piece of equipment, only to find out that their electrical service and / or wiring is insufficient. The repair Technicians quickly become frustrated with the (perceived) lack of performance of the machine and they resort to their old ways of repairing collision damaged vehicles.
When making the decision to invest in a STRSW machine, it's important that you work with the equipment maker and/or distributor to ensure that your facility is equipped with the necessary power to run the machine effectively. This may result in you also needing to contact your electrical service provider and making an infrastructure investment, in addition to your equipment investment. Pairing good equipment with the required electrical power is the only way to ensure that your welds are quality welds.
If you're looking to make the investment in a STRSW machine, you'll likely want to look for equipment that offers inverter technology, capable of supplying sufficient current for the number and thickness of the panels being welded, while producing the required squeeze force at the electrode tips. Some STRSW machine makers also offer machines that are pre programed with specific vehicle applications (material type and thickness), to allow for proper machine settings. These programs may include welding in pulse, or a slope-up and slope-down type of weld cycle and may include pre-set weld parameters for welding on specific vehicles.
MIG Brazing
Earlier, it was noted that Honda requires MIG brazing for areas on 1,500 MPa steel not accessible with spot welding arms. There are at least 10 locations on each B-pillar reinforcement that require MIG brazing and an additional handful on the lower A-pillar. The Acura MDX also uses 1,500 MPa steel to reinforce the door ring. Unlike the Accord's multiple piece reinforcements, the MDX uses a single 1,500 MPa stamping to reinforce the front door, to enhance occupant protection. This 1,500 MPa door ring is (at the time of this writing) the largest single stamping of this strength material used on any production vehicle.
Similar to the Accord, only STRSW and MIG brazing are permitted for installation of the door ring. Additionally, a number of other Honda and Acura vehicles are also employing 1,500 MPa steel in the side structures of their vehicles. Testing by Honda has shown that MIG brazing done in the pulse mode has higher strength. Therefore, in order to properly repair most late model Honda & Acura vehicles, a welder capable of pulse MIG brazing is required.
While MIG brazing is unfamiliar to most collision repairers in the U.S. and not widely required for repair of vehicles available in this market, the process is quite common in Europe and other markets around the world. There are some U.S. vehicle makers that allow MIG brazing on their vehicles, but don't currently require its use, or specify whether pulse, rather than short-circuit transfer, is required. For example, both Ford and General Motors allow MIG brazing to be used for a number of applications on their vehicles, for almost every type of steel, other than laminated steel, found on their vehicles.
Similar to aluminum welding, MIG brazing will require new equipment, or an adaptation of existing equipment, and training to ensure collision repair Technicians are readied to install parts using this technology. Also, similar to aluminum welding, MIG brazing requirements often include pulse welding technology and 100% argon shielding gas, as opposed to the 75/25% argon/CO2 mixture (C25) used for the vast majority of steel GMA (MIG) welding applications. This training will ensure that the technician understands how to set the machine to limit the amount of heat that will be transferred into heat sensitive steels, while producing a strong joint.
Vehicle Advancement Readiness
The advancements in vehicles and what's coming down the road – in addition to what's required to repair them -- will only get more complex. Staying current with training and equipping your facility with the proper tools and equipment is critical to your business and to your customers.
The I-CAR Welding Training & Certification™ program includes instruction on welding theory, a hands-on evaluation by the Instructor of the facility's gear, equipment and infrastructure prior to the in-shop training, practice and the industry-recognized certification test. Pricing for welding training has been reduced to make it more affordable for every Technician to have the hands-on training needed to complete a proper weld.
(A growing number of OEMs including Acura, Audi, Chrysler, Ford, GM, Honda, Infiniti, Jaguar, Land Rover, Lexus, Nissan, Porsche, Scion, Toyota, Volvo and Volkswagen include I-CAR Welding Training & Certification in their network programs.)
Whether it's steel, aluminum, other vehicle construction materials, or a combination of materials, it's important that you equip your facility with the proper tools, equipment and training to allow for complete, safe and quality repairs. These investments can lead to increased profitability, improved operational efficiency and productivity and higher customer satisfaction and retention levels.
Jason Bartanen is the I-CAR Director of Industry Technical Relations and is responsible for the I-CAR Repairability Technical Support initiative, at the I-CAR Tech Center in Appleton, WI. He has over 25 in the collision repair industry, the last 18 with I-CAR. Prior to his current role, Bartanen served several roles at I-CAR; as an Instructional Designer, Technical Development Manager and most recently as the Technical Director. Bartanen also assists in managing I-CAR’s specialty training development and delivery programs for a number of vehicle manufactures. Bartanen is a member of the SkillsUSA Collision Repair Technology committee.
*Used with the permission from Fixed Ops Magazine
Additional I-CAR Collision Repair News you may find helpful:
Related I-CAR Courses
-
Toyota/Lexus/Scion Position Statement: Pre- and Post-Repair System Scanning
Thursday, 28 July 2016
As the industry continues to ask if pre- and post-repair system scanning is necessary, Toyota/Lexus/Scion provides their answer.
-
Pre- and Post-Repair System Scanning Statements
Wednesday, 9 January 2019
Are you wondering if a particular OEM or organization has a published statement on pre-repair and post-repair scanning? We have compiled a list of most of the statements on the subject, so you can...
-
ADAS, Calibration, And Scanning Article Hotspot
Monday, 14 January 2019
Since advanced driver assistance systems (ADAS), scanning, and calibration first started becoming relevant, members of the collision repair industry have required as much knowledge as possible on...
-
Honda/Acura Position Statement: Pre- and Post-Repair System Scanning - UPDATE
Wednesday, 22 May 2019
Honda /Acura has updated their position statement on pre- and post-repair scanning to give more clarification on what is expected for scanning.
-
BMW Position Statement: Pre- and Post-Repair System Scanning - UPDATE
Friday, 10 April 2020
BMW has released a position statement related to pre- and post-repair system scanning. The statement applies to All vehicles equipped with on board diagnostics II (OBD II).
-
Quickly Identifying Outer Quarter Panels w/Rolled Hem Flanges
Monday, 5 March 2018
The I-CAR best practice article, Recycled Outer Quarter Panels w/Rolled Hem Flanges has gotten a lot of interest from the collision repair industry. It’s important to know which vehicles are...
-
General Motors Position Statement: Pre- and Post-Repair System Scanning
Friday, 21 October 2016
As the industry continues to ask, are pre- and post-repair scans necessary, General Motors provides their answer.
-
Restraints Wiring Repairs
Monday, 23 May 2016
Over the past few months, we've been sharing OEM position statements on restraints wiring repairs. Now we're bringing them all together in one place for easy reference.
-
FCA/Stellantis Position Statement: Pre- and Post-Repair System Scanning
Thursday, 9 June 2016
FCA/Stellantis has released a position statement related to pre- and post-repair system scanning.
-
Nissan/INFINITI Position Statement: Pre- and Post-Repair System Scanning - UPDATE
Monday, 14 January 2019
Nissan/INFINITI updated their position statement on pre- and post-repair scanning. The revised position statement touches on more subjects and gives additional information on the subject.
-
Repairer Driven News: Rivian Updates Door Handle Procedure
Sunday, 4 February 2035
Repairer Driven News (RDN) released an article featuring an updated Rivian procedure.
-
App-Based Connected Services Considerations: Ford/Lincoln
Tuesday, 19 August 2025
Have you had the experience where the vehicle notified the owner that it was being moved while it was in your repair facility? App-based connected services are available from many vehicle makers and may...
-
Digital Key Considerations: Ford/Lincoln
Tuesday, 19 August 2025
The intermingling of technology and automobiles continues, with digital key offerings from most vehicle makers. Digital keys utilize smartphone technology to expand vehicle access and owner...
-
Volkswagen Restraints Wiring - UPDATE
Thursday, 14 August 2025
The question is often asked, "Can supplemental restraints system wiring be repaired?" The answer is: it depends on the vehicle maker. Let's take a look at Volkswagen's position on this subject.
-
Jaguar Land Rover Restraints Wiring - UPDATE
Thursday, 14 August 2025
The question is often asked, "Can supplemental restraints system wiring be repaired?" The answer is: it depends on the vehicle maker. Let's take a look at Jaguar Land Rover's position on this subject.
-
I-CAR Repairers Realm: GMA Welding Machine Technology, Setup, And Maintenance - Coming Soon
Wednesday, 13 August 2025
I-CAR is having a discussion on GMA Welding Machine Technology, Setup, And Maintenance.
-
Great Designs In Steel 2025 Presentations: A Closer Look At The VW ID.Buzz Body-In-White Construction
Friday, 8 August 2025
In case you missed it, Eike Schuppert presented the VW ID.Buzz Body-In-White Construction at Great Designs in Steel 2025.
-
Backup Battery And Low-Voltage Disconnect
Wednesday, 6 August 2025
When an accident happens, how will you call for help? Maybe the telematics system, equipped with a backup battery, could automatically do this, even if the main power is cut off. What are the repair...
-
Backup Battery And Low Voltage Disconnect: Kia
Wednesday, 6 August 2025
When an accident happens, how will you call for help? Maybe the telematics system, equipped with a backup battery, could automatically do this, even if the main power is cut off. What are the repair...
-
OEM-Approved Connector And Pigtail Repair Resources: Jaguar Land Rover
Friday, 1 August 2025
When confronted with a wiring harness repair, we often struggle to find the correct connector and pigtail repair kits. Often, a specific connector may be used on multiple applications. If the...
- 2025
- August 2025 (9)
- July 2025 (11)
- June 2025 (11)
- May 2025 (11)
- April 2025 (13)
- March 2025 (11)
- February 2025 (11)
- January 2025 (12)
- 2024
- December 2024 (8)
- November 2024 (11)
- October 2024 (13)
- September 2024 (10)
- August 2024 (12)
- July 2024 (11)
- June 2024 (9)
- May 2024 (13)
- April 2024 (12)
- March 2024 (12)
- February 2024 (12)
- January 2024 (10)
- 2023
- December 2023 (8)
- November 2023 (12)
- October 2023 (11)
- September 2023 (11)
- August 2023 (12)
- July 2023 (9)
- June 2023 (11)
- May 2023 (12)
- April 2023 (11)
- March 2023 (12)
- February 2023 (10)
- January 2023 (11)
- 2022
- December 2022 (11)
- November 2022 (12)
- October 2022 (11)
- September 2022 (13)
- August 2022 (11)
- July 2022 (10)
- June 2022 (13)
- May 2022 (11)
- April 2022 (12)
- March 2022 (10)
- February 2022 (11)
- January 2022 (13)
- 2021
- December 2021 (13)
- November 2021 (11)
- October 2021 (13)
- September 2021 (14)
- August 2021 (12)
- July 2021 (15)
- June 2021 (17)
- May 2021 (14)
- April 2021 (14)
- March 2021 (20)
- February 2021 (14)
- January 2021 (14)
- 2020
- December 2020 (13)
- November 2020 (17)
- October 2020 (12)
- September 2020 (14)
- August 2020 (11)
- July 2020 (18)
- June 2020 (16)
- May 2020 (14)
- April 2020 (20)
- March 2020 (12)
- February 2020 (13)
- January 2020 (14)
- 2019
- December 2019 (13)
- November 2019 (19)
- October 2019 (25)
- September 2019 (20)
- August 2019 (22)
- July 2019 (23)
- June 2019 (20)
- May 2019 (19)
- April 2019 (20)
- March 2019 (20)
- February 2019 (18)
- January 2019 (18)
- 2018
- December 2018 (19)
- November 2018 (19)
- October 2018 (17)
- September 2018 (16)
- August 2018 (21)
- July 2018 (20)
- June 2018 (21)
- May 2018 (17)
- April 2018 (19)
- March 2018 (21)
- February 2018 (15)
- January 2018 (20)
- 2017
- December 2017 (13)
- November 2017 (15)
- October 2017 (19)
- September 2017 (20)
- August 2017 (20)
- July 2017 (18)
- June 2017 (19)
- May 2017 (19)
- April 2017 (13)
- March 2017 (18)
- February 2017 (10)
- January 2017 (11)
- 2016
- December 2016 (9)
- November 2016 (14)
- October 2016 (21)
- September 2016 (10)
- August 2016 (11)
- July 2016 (8)
- June 2016 (10)
- May 2016 (6)
- April 2016 (11)
- March 2016 (12)
- February 2016 (11)
- January 2016 (8)
- 2015
- December 2015 (9)
- November 2015 (7)
- October 2015 (8)
- September 2015 (7)
- August 2015 (11)
- July 2015 (7)
- June 2015 (5)
- May 2015 (7)
- April 2015 (8)
- March 2015 (8)
- February 2015 (9)
- January 2015 (10)
- 2014
- December 2014 (12)
- November 2014 (7)
- October 2014 (11)
- September 2014 (10)
- August 2014 (9)
- July 2014 (12)
- June 2014 (9)
- May 2014 (12)
- April 2014 (9)
- March 2014 (6)
- February 2014 (1)
- January 2014 (26)