Necessary Culture Changes For The Blueprinting Process
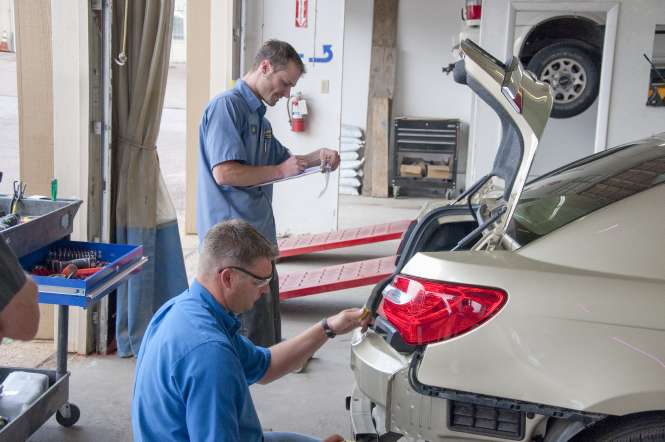
Blueprinting is a term often heard in the collision repair industry. Blueprinting means different things to different people, but blueprinting really is establishing a standard operating procedure (SOP) that allows for the discovery of all the damage before repairs begin. As part of the blueprinting process, all the parts should be identified right down to the blend panels and the clips that are needed. The correct repair information should be found along with any color matching that needs to be done. Following these steps and others, before repairs begin, will eliminate the problems that arise from finding additional damage during the repair process, which can interrupt and delay the repairs on that vehicle. Worse yet, is when the vehicle is repaired incorrectly because vehicle maker repair procedures were not followed.
One of the biggest challenges to implementing the blueprinting process may be the staff's perception of what will be involved. To be successful, those perceptions must be changed.
Changing Staff Perceptions
The blueprinting process requires a culture change throughout the repair facility. It also requires input from the entire team, not just management, to be successful. To change the culture, it may take some time for everyone to get onboard with the changes. When people become accustomed to their routine, they tend to resist change. They may feel that the new system will affect their efficiency and the work they produce. That is one of the reasons to implement small changes at first, so that the people who are resistant to making the changes can see positive results immediately.
It is also important to change the staff's thought process from being an individual to a team concept (see Figure 1). This is where everyone involved in the repair process is responsible for all the repairs of all the vehicles, not just the person who did a particular task. This does not mean that everyone does the same tasks or needs to work on all the vehicles that come through the repair facility. What this does mean is that the words "that's not my job" should be eliminated from everyone's vocabulary. By changing to a team approach, when one person is struggling with something, there is always someone to offer assistance or guidance.
The people involved in the blueprinting process also need to understand that one of the main concepts of blueprinting is rearranging the order of the steps necessary to repair a vehicle. For example, the "extra work" at the beginning of the repair process may be incorrectly perceived as additional work. However, in reality it is work that was traditionally done throughout the repair. By doing this work in the beginning, all of the repairs can be completed in a complete, efficient, and timely manner. An example of this would be disassembling a blend panel before the vehicle enters the repair technician's stall, and finding that a door molding is a one-time use molding. By identifying this one-time use molding in the beginning of repairs, it allows the part to be ordered and prevent the vehicle from being delayed due to a missing part.
Some staff members may not be willing to make the necessary changes to the new blueprinting process. In this case, the person in charge may have to make some hard decisions. If this person can be convinced to try the changes, they'll most likely get onboard with the changes. If the person refuses to change what they've always done, the blueprinting process will be difficult, if not impossible to implement. Unfortunately, it may end in the manager and technician deciding to part ways; this is never an easy decision.
Figure 2 - An estimator is taking preliminary measurements using the Matrix Wand measuring system.A disassembly blueprint estimator is an example of one of the many options for implementing the blueprinting process. With this option, the person that does the disassembly is also the one submitting the completed damage report. Another option is a dedicated technician and estimator working together in a dedicated stall. This system allows for the two people to develop an SOP so that they can be consistent in the blueprinting process.
How blueprinting is implemented will be influenced by the size and configuration of the repair facility (see Figure 2). Whatever system will work in the repair facility is what should be implemented. While all vehicles and collisions are different, the blueprinting process for each repair can remain consistent. It is important that once the process starts, the same blueprinting process must be followed on each vehicle. However, this does not mean that the blueprinting process cannot evolve and change. Once the blueprinting process is in place, there will be steps in the process that may require modification and improvement.
Conclusion
The biggest challenge to implementing the blueprinting process may be the staff's perception of what will be involved. We have discussed how changing perceptions is an important step to the successful implementation of the blueprinting process. The goal is that once the blueprinting process is implemented, there will be complete and safe repairs on time every time.
This article first appeared in the December 3, 2012 edition of the I-CAR Advantage Online.
Related I-CAR Courses
-
Toyota/Lexus/Scion Position Statement: Pre- and Post-Repair System Scanning
Thursday, 28 July 2016
As the industry continues to ask if pre- and post-repair system scanning is necessary, Toyota/Lexus/Scion provides their answer.
-
Pre- and Post-Repair System Scanning Statements
Wednesday, 9 January 2019
Are you wondering if a particular OEM or organization has a published statement on pre-repair and post-repair scanning? We have compiled a list of most of the statements on the subject, so you can...
-
ADAS, Calibration, And Scanning Article Hotspot
Monday, 14 January 2019
Since advanced driver assistance systems (ADAS), scanning, and calibration first started becoming relevant, members of the collision repair industry have required as much knowledge as possible on...
-
Honda/Acura Position Statement: Pre- and Post-Repair System Scanning - UPDATE
Wednesday, 22 May 2019
Honda /Acura has updated their position statement on pre- and post-repair scanning to give more clarification on what is expected for scanning.
-
BMW Position Statement: Pre- and Post-Repair System Scanning - UPDATE
Friday, 10 April 2020
BMW has released a position statement related to pre- and post-repair system scanning. The statement applies to All vehicles equipped with on board diagnostics II (OBD II).
-
Quickly Identifying Outer Quarter Panels w/Rolled Hem Flanges
Monday, 5 March 2018
The I-CAR best practice article, Recycled Outer Quarter Panels w/Rolled Hem Flanges has gotten a lot of interest from the collision repair industry. It’s important to know which vehicles are...
-
General Motors Position Statement: Pre- and Post-Repair System Scanning
Friday, 21 October 2016
As the industry continues to ask, are pre- and post-repair scans necessary, General Motors provides their answer.
-
Restraints Wiring Repairs
Monday, 23 May 2016
Over the past few months, we've been sharing OEM position statements on restraints wiring repairs. Now we're bringing them all together in one place for easy reference.
-
FCA/Stellantis Position Statement: Pre- and Post-Repair System Scanning
Thursday, 9 June 2016
FCA/Stellantis has released a position statement related to pre- and post-repair system scanning.
-
Nissan/INFINITI Position Statement: Pre- and Post-Repair System Scanning - UPDATE
Monday, 14 January 2019
Nissan/INFINITI updated their position statement on pre- and post-repair scanning. The revised position statement touches on more subjects and gives additional information on the subject.
-
Repairer Driven News: Rivian Updates Door Handle Procedure
Sunday, 4 February 2035
Repairer Driven News (RDN) released an article featuring an updated Rivian procedure.
-
App-Based Connected Services Considerations: Ford/Lincoln
Tuesday, 19 August 2025
Have you had the experience where the vehicle notified the owner that it was being moved while it was in your repair facility? App-based connected services are available from many vehicle makers and may...
-
Digital Key Considerations: Ford/Lincoln
Tuesday, 19 August 2025
The intermingling of technology and automobiles continues, with digital key offerings from most vehicle makers. Digital keys utilize smartphone technology to expand vehicle access and owner...
-
Volkswagen Restraints Wiring - UPDATE
Thursday, 14 August 2025
The question is often asked, "Can supplemental restraints system wiring be repaired?" The answer is: it depends on the vehicle maker. Let's take a look at Volkswagen's position on this subject.
-
Jaguar Land Rover Restraints Wiring - UPDATE
Thursday, 14 August 2025
The question is often asked, "Can supplemental restraints system wiring be repaired?" The answer is: it depends on the vehicle maker. Let's take a look at Jaguar Land Rover's position on this subject.
-
I-CAR Repairers Realm: GMA Welding Machine Technology, Setup, And Maintenance - Coming Soon
Wednesday, 13 August 2025
I-CAR is having a discussion on GMA Welding Machine Technology, Setup, And Maintenance.
-
Great Designs In Steel 2025 Presentations: A Closer Look At The VW ID.Buzz Body-In-White Construction
Friday, 8 August 2025
In case you missed it, Eike Schuppert presented the VW ID.Buzz Body-In-White Construction at Great Designs in Steel 2025.
-
Backup Battery And Low-Voltage Disconnect
Wednesday, 6 August 2025
When an accident happens, how will you call for help? Maybe the telematics system, equipped with a backup battery, could automatically do this, even if the main power is cut off. What are the repair...
-
Backup Battery And Low Voltage Disconnect: Kia
Wednesday, 6 August 2025
When an accident happens, how will you call for help? Maybe the telematics system, equipped with a backup battery, could automatically do this, even if the main power is cut off. What are the repair...
-
OEM-Approved Connector And Pigtail Repair Resources: Jaguar Land Rover
Friday, 1 August 2025
When confronted with a wiring harness repair, we often struggle to find the correct connector and pigtail repair kits. Often, a specific connector may be used on multiple applications. If the...
- 2025
- August 2025 (9)
- July 2025 (11)
- June 2025 (11)
- May 2025 (11)
- April 2025 (13)
- March 2025 (11)
- February 2025 (11)
- January 2025 (12)
- 2024
- December 2024 (8)
- November 2024 (11)
- October 2024 (13)
- September 2024 (10)
- August 2024 (12)
- July 2024 (11)
- June 2024 (9)
- May 2024 (13)
- April 2024 (12)
- March 2024 (12)
- February 2024 (12)
- January 2024 (10)
- 2023
- December 2023 (8)
- November 2023 (12)
- October 2023 (11)
- September 2023 (11)
- August 2023 (12)
- July 2023 (9)
- June 2023 (11)
- May 2023 (12)
- April 2023 (11)
- March 2023 (12)
- February 2023 (10)
- January 2023 (11)
- 2022
- December 2022 (11)
- November 2022 (12)
- October 2022 (11)
- September 2022 (13)
- August 2022 (11)
- July 2022 (10)
- June 2022 (13)
- May 2022 (11)
- April 2022 (12)
- March 2022 (10)
- February 2022 (11)
- January 2022 (13)
- 2021
- December 2021 (13)
- November 2021 (11)
- October 2021 (13)
- September 2021 (14)
- August 2021 (12)
- July 2021 (15)
- June 2021 (17)
- May 2021 (14)
- April 2021 (14)
- March 2021 (20)
- February 2021 (14)
- January 2021 (14)
- 2020
- December 2020 (13)
- November 2020 (17)
- October 2020 (12)
- September 2020 (14)
- August 2020 (11)
- July 2020 (18)
- June 2020 (16)
- May 2020 (14)
- April 2020 (20)
- March 2020 (12)
- February 2020 (13)
- January 2020 (14)
- 2019
- December 2019 (13)
- November 2019 (19)
- October 2019 (25)
- September 2019 (20)
- August 2019 (22)
- July 2019 (23)
- June 2019 (20)
- May 2019 (19)
- April 2019 (20)
- March 2019 (20)
- February 2019 (18)
- January 2019 (18)
- 2018
- December 2018 (19)
- November 2018 (19)
- October 2018 (17)
- September 2018 (16)
- August 2018 (21)
- July 2018 (20)
- June 2018 (21)
- May 2018 (17)
- April 2018 (19)
- March 2018 (21)
- February 2018 (15)
- January 2018 (20)
- 2017
- December 2017 (13)
- November 2017 (15)
- October 2017 (19)
- September 2017 (20)
- August 2017 (20)
- July 2017 (18)
- June 2017 (19)
- May 2017 (19)
- April 2017 (13)
- March 2017 (18)
- February 2017 (10)
- January 2017 (11)
- 2016
- December 2016 (9)
- November 2016 (14)
- October 2016 (21)
- September 2016 (10)
- August 2016 (11)
- July 2016 (8)
- June 2016 (10)
- May 2016 (6)
- April 2016 (11)
- March 2016 (12)
- February 2016 (11)
- January 2016 (8)
- 2015
- December 2015 (9)
- November 2015 (7)
- October 2015 (8)
- September 2015 (7)
- August 2015 (11)
- July 2015 (7)
- June 2015 (5)
- May 2015 (7)
- April 2015 (8)
- March 2015 (8)
- February 2015 (9)
- January 2015 (10)
- 2014
- December 2014 (12)
- November 2014 (7)
- October 2014 (11)
- September 2014 (10)
- August 2014 (9)
- July 2014 (12)
- June 2014 (9)
- May 2014 (12)
- April 2014 (9)
- March 2014 (6)
- February 2014 (1)
- January 2014 (26)