General Motors Overlap Sectioning Joint
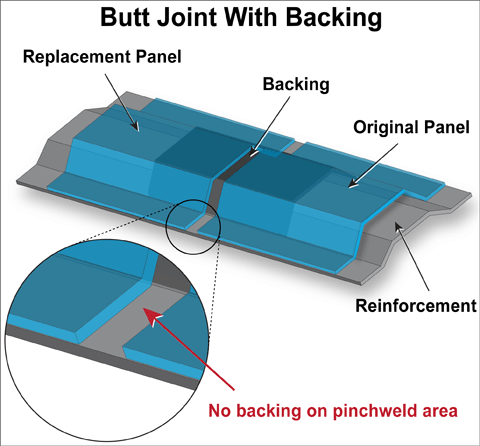
Until recently, General Motors has generally specified butt joints with backings when sectioning parts of a uniside. However, an overlap joint is now being required for some uniside sectioning joints. This is being done to reduce the transfer of heat from GMA welding into heat-sensitive high- and ultra-high-strength steel reinforcements. The concern with a butt joint with backing is that the backing piece does not extend to the pinchweld flange, and leaves the reinforcement exposed. As a result, a GMA weld is made on the pinchweld flange area of the reinforcement (see Figure 1).
Overlap Joint
The overlap joint specified in some new General Motors repair procedures is made by cutting the replacement part to overlap the original part on the vehicle 25 mm (1"). The overlap allows the original panel to serve as a backing for the seam weld, even on the pinchweld flanges, better protecting the reinforcement from the heat of the weld (see Figure 2). This is also a less complicated process compared to a butt joint with backing, and reduces the chance for cutting the replacement part too short.
Figure 2 - The original panel serves as a backing, and protects the reinforcement from welding heat.
The overlap joint was first specified for the outer rocker panel on the 2010 Chevrolet Camaro, and is mentioned in a previous I-CAR Advantage Online article, "Collision Repair For The 2010 Chevrolet Camaro." Since then, an overlap joint has been specified for various sectioning joints on the 2011 Chevrolet Volt, 2011 Buick Regal, and 2012 Chevrolet Sonic. Common procedures this type of joint is used for include replacement of the outer A-pillar, rocker panel, B-pillar, and quarter panel.
Welding
The overlap joint is welded using a fillet weld. Plug welds may be required as well, but this recommendation varies according to the procedure. The fillet weld should be made using a skip or stitch technique to minimize the chance for heat distortion. This is done by making 25 mm (1") welds along the seam with 25 mm (1") gaps between each weld, and then going back to fill in the gaps (See Figure 3).
Conclusion
Figure 3 - The first set of seam welds should leave a 25 mm (1") gap between each weld. The second set of seam welds fill in the gaps.A butt joint with backing is not always specified for sectioning procedures on General Motors vehicles anymore. It is becoming more common for sectioning procedures to specify an overlap joint when sectioning parts of a uniside. This is why it is so important to always refer to the vehicle maker procedures to ensure the correct joint is being used. Collision repair procedures for General Motors vehicles can be accessed at acdelcotds.com.
This article first appeared in the May 31, 2012 edition of the I-CAR Advantage Online.
For additional links to GM, check out the following pages:
Chevrolet OEM Information
GMC OEM Information
Buick OEM Information
Cadillac OEM Information
Additional I-CAR Collision Repair News you may find helpful:
- Collision Information Website Access: General Motors
- Step-By-Step: Accessing General Motors Repair Information
Related I-CAR Courses
-
Toyota/Lexus/Scion Position Statement: Pre- and Post-Repair System Scanning
Thursday, 28 July 2016
As the industry continues to ask if pre- and post-repair system scanning is necessary, Toyota/Lexus/Scion provides their answer.
-
Pre- and Post-Repair System Scanning Statements
Wednesday, 9 January 2019
Are you wondering if a particular OEM or organization has a published statement on pre-repair and post-repair scanning? We have compiled a list of most of the statements on the subject, so you can...
-
ADAS, Calibration, And Scanning Article Hotspot
Monday, 14 January 2019
Since advanced driver assistance systems (ADAS), scanning, and calibration first started becoming relevant, members of the collision repair industry have required as much knowledge as possible on...
-
Honda/Acura Position Statement: Pre- and Post-Repair System Scanning - UPDATE
Wednesday, 22 May 2019
Honda /Acura has updated their position statement on pre- and post-repair scanning to give more clarification on what is expected for scanning.
-
BMW Position Statement: Pre- and Post-Repair System Scanning - UPDATE
Friday, 10 April 2020
BMW has released a position statement related to pre- and post-repair system scanning. The statement applies to All vehicles equipped with on board diagnostics II (OBD II).
-
Quickly Identifying Outer Quarter Panels w/Rolled Hem Flanges
Monday, 5 March 2018
The I-CAR best practice article, Recycled Outer Quarter Panels w/Rolled Hem Flanges has gotten a lot of interest from the collision repair industry. It’s important to know which vehicles are...
-
General Motors Position Statement: Pre- and Post-Repair System Scanning
Friday, 21 October 2016
As the industry continues to ask, are pre- and post-repair scans necessary, General Motors provides their answer.
-
Restraints Wiring Repairs
Monday, 23 May 2016
Over the past few months, we've been sharing OEM position statements on restraints wiring repairs. Now we're bringing them all together in one place for easy reference.
-
FCA/Stellantis Position Statement: Pre- and Post-Repair System Scanning
Thursday, 9 June 2016
FCA/Stellantis has released a position statement related to pre- and post-repair system scanning.
-
Nissan/INFINITI Position Statement: Pre- and Post-Repair System Scanning - UPDATE
Monday, 14 January 2019
Nissan/INFINITI updated their position statement on pre- and post-repair scanning. The revised position statement touches on more subjects and gives additional information on the subject.
-
Repairer Driven News: Rivian Updates Door Handle Procedure
Sunday, 4 February 2035
Repairer Driven News (RDN) released an article featuring an updated Rivian procedure.
-
GM Part Replacement Without A Procedure
Friday, 22 August 2025
We are often asked, “What do I do if there isn’t a procedure to replace a service part?” Let’s see what GM says.
-
App-Based Connected Services Considerations: Ford/Lincoln
Tuesday, 19 August 2025
Have you had the experience where the vehicle notified the owner that it was being moved while it was in your repair facility? App-based connected services are available from many vehicle makers and may...
-
Digital Key Considerations: Ford/Lincoln
Tuesday, 19 August 2025
The intermingling of technology and automobiles continues, with digital key offerings from most vehicle makers. Digital keys utilize smartphone technology to expand vehicle access and owner...
-
Volkswagen Restraints Wiring - UPDATE
Thursday, 14 August 2025
The question is often asked, "Can supplemental restraints system wiring be repaired?" The answer is: it depends on the vehicle maker. Let's take a look at Volkswagen's position on this subject.
-
Jaguar Land Rover Restraints Wiring - UPDATE
Thursday, 14 August 2025
The question is often asked, "Can supplemental restraints system wiring be repaired?" The answer is: it depends on the vehicle maker. Let's take a look at Jaguar Land Rover's position on this subject.
-
I-CAR Repairers Realm: GMA Welding Machine Technology, Setup, And Maintenance - Coming Soon
Wednesday, 13 August 2025
I-CAR is having a discussion on GMA Welding Machine Technology, Setup, And Maintenance.
-
Great Designs In Steel 2025 Presentations: A Closer Look At The VW ID.Buzz Body-In-White Construction
Friday, 8 August 2025
In case you missed it, Eike Schuppert presented the VW ID.Buzz Body-In-White Construction at Great Designs in Steel 2025.
-
Backup Battery And Low-Voltage Disconnect
Wednesday, 6 August 2025
When an accident happens, how will you call for help? Maybe the telematics system, equipped with a backup battery, could automatically do this, even if the main power is cut off. What are the repair...
-
Backup Battery And Low Voltage Disconnect: Kia
Wednesday, 6 August 2025
When an accident happens, how will you call for help? Maybe the telematics system, equipped with a backup battery, could automatically do this, even if the main power is cut off. What are the repair...
- 2025
- August 2025 (10)
- July 2025 (11)
- June 2025 (11)
- May 2025 (11)
- April 2025 (13)
- March 2025 (11)
- February 2025 (11)
- January 2025 (12)
- 2024
- December 2024 (8)
- November 2024 (11)
- October 2024 (13)
- September 2024 (10)
- August 2024 (12)
- July 2024 (11)
- June 2024 (9)
- May 2024 (13)
- April 2024 (12)
- March 2024 (12)
- February 2024 (12)
- January 2024 (10)
- 2023
- December 2023 (8)
- November 2023 (12)
- October 2023 (11)
- September 2023 (11)
- August 2023 (12)
- July 2023 (9)
- June 2023 (11)
- May 2023 (12)
- April 2023 (11)
- March 2023 (12)
- February 2023 (10)
- January 2023 (11)
- 2022
- December 2022 (11)
- November 2022 (12)
- October 2022 (11)
- September 2022 (13)
- August 2022 (11)
- July 2022 (10)
- June 2022 (13)
- May 2022 (11)
- April 2022 (12)
- March 2022 (10)
- February 2022 (11)
- January 2022 (13)
- 2021
- December 2021 (13)
- November 2021 (11)
- October 2021 (13)
- September 2021 (14)
- August 2021 (12)
- July 2021 (15)
- June 2021 (17)
- May 2021 (14)
- April 2021 (14)
- March 2021 (20)
- February 2021 (14)
- January 2021 (14)
- 2020
- December 2020 (13)
- November 2020 (17)
- October 2020 (12)
- September 2020 (14)
- August 2020 (11)
- July 2020 (18)
- June 2020 (16)
- May 2020 (14)
- April 2020 (20)
- March 2020 (12)
- February 2020 (13)
- January 2020 (14)
- 2019
- December 2019 (13)
- November 2019 (19)
- October 2019 (25)
- September 2019 (20)
- August 2019 (22)
- July 2019 (23)
- June 2019 (20)
- May 2019 (19)
- April 2019 (20)
- March 2019 (20)
- February 2019 (18)
- January 2019 (18)
- 2018
- December 2018 (19)
- November 2018 (19)
- October 2018 (17)
- September 2018 (16)
- August 2018 (21)
- July 2018 (20)
- June 2018 (21)
- May 2018 (17)
- April 2018 (19)
- March 2018 (21)
- February 2018 (15)
- January 2018 (20)
- 2017
- December 2017 (13)
- November 2017 (15)
- October 2017 (19)
- September 2017 (20)
- August 2017 (20)
- July 2017 (18)
- June 2017 (19)
- May 2017 (19)
- April 2017 (13)
- March 2017 (18)
- February 2017 (10)
- January 2017 (11)
- 2016
- December 2016 (9)
- November 2016 (14)
- October 2016 (21)
- September 2016 (10)
- August 2016 (11)
- July 2016 (8)
- June 2016 (10)
- May 2016 (6)
- April 2016 (11)
- March 2016 (12)
- February 2016 (11)
- January 2016 (8)
- 2015
- December 2015 (9)
- November 2015 (7)
- October 2015 (8)
- September 2015 (7)
- August 2015 (11)
- July 2015 (7)
- June 2015 (5)
- May 2015 (7)
- April 2015 (8)
- March 2015 (8)
- February 2015 (9)
- January 2015 (10)
- 2014
- December 2014 (12)
- November 2014 (7)
- October 2014 (11)
- September 2014 (10)
- August 2014 (9)
- July 2014 (12)
- June 2014 (9)
- May 2014 (12)
- April 2014 (9)
- March 2014 (6)
- February 2014 (1)
- January 2014 (26)