Insulated Rubber Gloves And High-Voltage Batteries
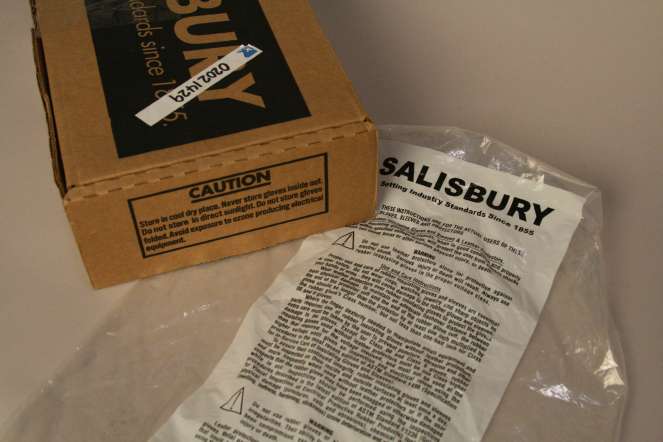
Ever since the requirement of wearing insulated rubber gloves, or lineman's gloves, when working on hybrid electric vehicles was introduced in vehicle service information, there have been questions. Are these really the same gloves worn by those who work with high-voltage power lines? Are these gloves necessary or are they overkill? Are these gloves only used for disabling and enabling the high-voltage? What does the U.S. Occupational Safety and Health Administration (OSHA) say about the use of these gloves?
This article is designed to answer these questions.
Class | Max AC Use Voltage | AC Retest Voltage | Maximum DC Use Voltage (average) | DC Retest Voltage (average) | Color of Label |
00 | 500 | 2,500 | 750 | 10,000 | Tan |
0 | 1,000 | 5,000 | 1,500 | 20,000 | Red |
1 | 7,500 | 10,000 | 11,250 | 40,000 | White |
2 | 17,500 | 20,000 | 25,500 | 50,000 | Yellow |
3 | 26,500 | 30,000 | 39,750 | 60,000 | Green |
4 | 36,000 | 40,000 | 54,000 | 70,000 | Orange |
Figure 1 - This chart shows the AC and DC voltage ratings for each class of insulated rubber gloves. |
Glove Requirement
Toyota is clear on when insulated rubber gloves should be worn. The vehicle maker states that the gloves should be worn "whenever working near high-voltage components. High-voltage components include the high-voltage battery, system main relay, service plug receptacle and fuse, orange-colored cables, inverter assembly, electric drive motors, DC-DC converter, and the electric air conditioning compressor." In other words, the gloves are not just worn when disabling and enabling the high-voltage battery.
There are several classes for insulated rubber gloves, from Class 00 to Class 4, depending on the maximum use voltage that the gloves can withstand (see Figure 1). It is generally accepted by the vehicle makers that Class 0 gloves are a good choice when working on hybrid electric vehicles, as they are rated at 1,500 volts DC maximum use voltage. Class 0 gloves are solid black in color.
Figure 2 - Requirements for testing and care for the gloves are outlined on the plastic bag and box where the gloves are packaged.Why is the vehicle maker service information limited as to the care and testing of these gloves? Vehicle makers expect technicians to follow the instructions and requirements from the glove manufacturer. These are commonly printed on the box and the plastic bag the gloves are shipped in (see Figure 2). Among the requirements printed on the bag label are the use of leather protective outers, testing requirements, and protecting the gloves from chemicals and other contamination. On the outside of the box, there are precautions to not store the gloves inside out, folded, or in direct sunlight.
OSHA addresses the testing, use, and care of rubber insulating gloves in the Personal Protective Equipment Standard 1910.137, Electrical Protective Devices. There are more details in the American Society for Testing and Materials (ASTM) Standard Specification for In-Service Care of Insulating Gloves and Sleeves.
Glove Label
Figure 3 - There is several information on a label on the cuff of each glove.In the cuff portion of each glove, there's a nonconductive label (see Figure 3). As listed in the table in Figure 1, the label is colored depending on the glove class. Information on the label may include the glove manufacturer, the class, and the rated maximum-use voltage. The AC voltage rating is only listed on the label, since these gloves are more commonly used when working with AC voltages. The label will also indicate if the gloves are resistant to ozone (Type II) or non-ozone resistant (Type I).
The label may indicate the glove size. Insulated rubber gloves are not one-size-fits all. They should be purchased based on the hand size of the technician who will be wearing them. For some glove manufacturers, there are only three choices: small, medium, and large. Other manufacturers offer half sizes, in inches. To find your measurement, lay your hand palm down on Figure 4 - To find the size glove for you, measure your hand around the knuckle area and add one inch.a flat surface and measure the circumference around your finger knuckles (see Figure 4). Add one inch to that measurement, and that is your hand size for insulated rubber gloves.
Storage
Proper storage is important to help keep the gloves in good condition. The gloves should be stored in a location as cool, dark, and dry as possible. The location should be as free as practicable from ozone, chemicals, oils, solvents, damaging vapors or fumes, and away from electrical discharges and sunlight. Fluorescent light and sunlight are especially harmful to rubber.
The gloves should be stored flat, not folded, and not in any manner that will cause stretching or compression. They should be kept inside a protective container or canvas bag. The original box that the gloves came in is also a good storage compartment for the gloves.
Inspection Before Use
OSHA requires that the technician who will use the insulated rubber gloves inspect the gloves for damage before each use, and immediately following any incident that can reasonably be suspected of having caused damage. If the inspection finds any of the following, the gloves should be discarded:
- Hole, tear, puncture, or cut
- Embedded foreign object
- Ozone checking, which looks like dry rot. Ozone checking is a series of interlacing cracks produced by ozone on rubber under mechanical stress.
- Texture changes caused by swelling, softening, hardening, or becoming sticky or inelastic
The gloves should be cleaned as needed to remove foreign substances. If any defect is found that might damage the insulating properties, such as spilled chemicals that do not wash off, the gloves should be submitted to a testing facility for testing.
Figure 5 - Insulated rubber gloves may be repaired, but only in the gauntlet area.Minor damage to the gloves can be repaired, but only in the area between the wrist and the reinforced edge of the opening, called the "gauntlet area" of the glove (see Figure 5). In this area, small cuts, tears, or punctures may be repaired by applying a compatible patch. Minor blemishes in this same area may be repaired with a compatible liquid compound. The patched area should have electrical and physical properties equal to those of the surrounding material. No more than three patches may be applied to one glove. Any gloves that are repaired should be retested by a testing facility before they are used.
OSHA also specifies that an air test should be done in the field before each use, and at other times if there is cause to suspect any damage. The ASTM standard specifies that an air test can be done by holding the glove by the cuff and rolling the gloves gently toward the fingers to form an air pocket inside the glove. While the air is entrapped, check the gloves for punctures or checking, listen for escaping air, and hold the gloves up against your cheek to feel for escaping air. If the glove will not hold pressure, the glove is damaged and should not be used. The air test can also be done with a mechanical inflator. On the higher classes of gloves, an inflator is required because the gloves are too stiff to be rolled up by hand.
Remove all jewelry before putting the gloves on. This is a common recommendation whenever working in a collision repair facility, but is of special importance here so as to not snag the gloves on rings or watches, etc., potentially damaging the gloves.
Protective Leather Outers
Insulated rubber gloves should be protected while being worn with protective leather outer gloves. OSHA excludes the limited use of Class 00 and Class 0 gloves from this requirement. That is because for most industries, these lighter gloves are used where high finger dexterity might be needed to handle small equipment and parts, and leather outers might be too bulky.
For most work on hybrid vehicles, however, leather outers are highly recommended by the glove manufacturers and vehicle makers. The leather helps prevent catching the rubber gloves on sharp sheet metal parts and frayed wiring, possibly puncturing the rubber.
The leather outers should be exclusive for this purpose. Do not use the leather outers as general use gloves. The leather outers should be sized and shaped so that the rubber glove is not deformed. The top of the cuff of the leather outer should be shorter than the rolled top of the insulated rubber glove by at least 13 mm (1/2 in).
The leather outers should be inspected just as often as inspection of the insulated rubber gloves. They should not have holes, tears, or other defects that affect their ability to give protection to the insulated rubber gloves. The inner surface of the leather outers should be inspected for sharp or pointed objects.
Care should be taken to keep the outers away from oils, greases, chemicals, solvents, and other materials that may damage the insulated rubber gloves. This also goes for the insulated rubber gloves.
Insulated rubber gloves are available from some manufacturers in kit form, which includes the leather outers and a canvas bag for storage.
Testing at a Testing Facility
Insulated rubber gloves are tested before being sold, but that's not the last test. The gloves should be tested every six months by an official testing facility. Once the gloves are removed from the plastic bag they were shipped in, they start to deteriorate. So even if they are used only once, they will require retesting in six months time. If the gloves were purchased, but not put into use for several months, retesting may be required before the gloves are even used for the first time. OSHA states that the gloves may not be used if they haven't been tested within the previous 12 months.
Find the nearest testing facility by doing an Internet search for "glove testing." The testing is not done differently depending on the facility you find. The ASTM standard includes requirements that every testing facility must follow. The standard requires that the testing facility:
- wash the gloves.
- do a preliminary inspection similar to what is done in the field.
- do a more detailed inspection which includes turning them inside out and may include inflating them with air.
- make any necessary repairs.
- do an electrical test.
Note in the table in Figure 1 that the electrical retest is at a higher-rated voltage than the initial test. The gloves are electrically tested while filled with water and immersed in a water bath. The test voltage is applied between one and three continuous minutes.
Once the testing is completed, the test facility may note the date of the test directly on the gloves. Employers are required to certify that the gloves have been tested in accordance with the OSHA requirements. This can be done by noting the results and dates of the test in a log, or by noting whether the test dates are printed on the gloves. The test facility we contacted does print the test dates directly on the gloves and maintains seven years of reports, which can be provided to the repair facility if ever needed.
Conclusion
Class 0 insulated rubber gloves, or lineman's gloves, are required whenever working near high-voltage parts on an electric or hybrid electric vehicle. There are strict requirements for using, protecting, storing, inspecting, and testing of these gloves. If you are a technician assigned to do work on one of these vehicles, become familiar with the glove requirements.
There are, of course, a lot more precautions that should be taken when working near high-voltage parts on an electric or hybrid electric vehicle beyond just the insulated rubber gloves. Vehicle makers also provide safety training for hybrid vehicles. Toyota, for example, offers instructor-led training courses "Toyota Hybrid Collision Repair" and "Toyota Prius Collision Repair" at three training sites in the U.S. For more information on this training, visit www.crrtraining.com.
We would like to give thanks to Kim Schneider, an independent electrical contractor based in Philadelphia, PA, for his assistance with alerting us to the multiple issues with these insulated rubber gloves.
This article first appeared in the February 2, 2010 edition of the I-CAR Advantage Online.
Additional I-CAR Collision Repair News you may find helpful:
Related I-CAR Courses
-
Toyota/Lexus/Scion Position Statement: Pre- and Post-Repair System Scanning
Thursday, 28 July 2016
As the industry continues to ask if pre- and post-repair system scanning is necessary, Toyota/Lexus/Scion provides their answer.
-
Pre- and Post-Repair System Scanning Statements
Wednesday, 9 January 2019
Are you wondering if a particular OEM or organization has a published statement on pre-repair and post-repair scanning? We have compiled a list of most of the statements on the subject, so you can...
-
ADAS, Calibration, And Scanning Article Hotspot
Monday, 14 January 2019
Since advanced driver assistance systems (ADAS), scanning, and calibration first started becoming relevant, members of the collision repair industry have required as much knowledge as possible on...
-
Honda/Acura Position Statement: Pre- and Post-Repair System Scanning - UPDATE
Wednesday, 22 May 2019
Honda /Acura has updated their position statement on pre- and post-repair scanning to give more clarification on what is expected for scanning.
-
BMW Position Statement: Pre- and Post-Repair System Scanning - UPDATE
Friday, 10 April 2020
BMW has released a position statement related to pre- and post-repair system scanning. The statement applies to All vehicles equipped with on board diagnostics II (OBD II).
-
Quickly Identifying Outer Quarter Panels w/Rolled Hem Flanges
Monday, 5 March 2018
The I-CAR best practice article, Recycled Outer Quarter Panels w/Rolled Hem Flanges has gotten a lot of interest from the collision repair industry. It’s important to know which vehicles are...
-
General Motors Position Statement: Pre- and Post-Repair System Scanning
Friday, 21 October 2016
As the industry continues to ask, are pre- and post-repair scans necessary, General Motors provides their answer.
-
Restraints Wiring Repairs
Monday, 23 May 2016
Over the past few months, we've been sharing OEM position statements on restraints wiring repairs. Now we're bringing them all together in one place for easy reference.
-
FCA/Stellantis Position Statement: Pre- and Post-Repair System Scanning
Thursday, 9 June 2016
FCA/Stellantis has released a position statement related to pre- and post-repair system scanning.
-
Nissan/INFINITI Position Statement: Pre- and Post-Repair System Scanning - UPDATE
Monday, 14 January 2019
Nissan/INFINITI updated their position statement on pre- and post-repair scanning. The revised position statement touches on more subjects and gives additional information on the subject.
-
Repairer Driven News: Rivian Updates Door Handle Procedure
Sunday, 4 February 2035
Repairer Driven News (RDN) released an article featuring an updated Rivian procedure.
-
Repairers Realm: GMA Welding Machine Technology, Setup, And Maintenance - Now Available
Tuesday, 2 September 2025
I-CAR had a discussion on GMA welding machine technology, setup, and maintenance.
-
Ford And Lincoln Restraints Wiring: UPDATE
Friday, 29 August 2025
The question is often asked, "Can supplemental restraints system wiring be repaired?" The answer is: it depends on the vehicle maker. Let's take a look at Ford's and Lincoln's position on this...
-
High-Voltage Vehicle Research Tips: GM BEV Low-Voltage Battery Disconnection
Thursday, 28 August 2025
While researching OEM repair information, you may come across specific notes, instructions, or warnings for high-voltage (HV) vehicles. Some general procedures can be easily overlooked, so it’s...
-
High-Voltage Vehicle Research Tips
Thursday, 28 August 2025
While researching OEM repair information, you may come across specific notes, instructions, or warnings for high-voltage (HV) vehicles. Some general procedures can be easily overlooked, so it’s...
-
GM Part Replacement Without A Procedure
Friday, 22 August 2025
We are often asked, “What do I do if there isn’t a procedure to replace a service part?” Let’s see what GM says.
-
App-Based Connected Services Considerations: Ford/Lincoln
Tuesday, 19 August 2025
Have you had the experience where the vehicle notified the owner that it was being moved while it was in your repair facility? App-based connected services are available from many vehicle makers and may...
-
Digital Key Considerations: Ford/Lincoln
Tuesday, 19 August 2025
The intermingling of technology and automobiles continues, with digital key offerings from most vehicle makers. Digital keys utilize smartphone technology to expand vehicle access and owner...
-
Volkswagen Restraints Wiring: UPDATE
Thursday, 14 August 2025
The question is often asked, "Can supplemental restraints system wiring be repaired?" The answer is: it depends on the vehicle maker. Let's take a look at Volkswagen's position on this subject.
-
Jaguar Land Rover Restraints Wiring: UPDATE
Thursday, 14 August 2025
The question is often asked, "Can supplemental restraints system wiring be repaired?" The answer is: it depends on the vehicle maker. Let's take a look at Jaguar Land Rover's position on this subject.
- 2025
- September 2025 (1)
- August 2025 (12)
- July 2025 (11)
- June 2025 (11)
- May 2025 (11)
- April 2025 (13)
- March 2025 (11)
- February 2025 (11)
- January 2025 (12)
- 2024
- December 2024 (8)
- November 2024 (11)
- October 2024 (13)
- September 2024 (10)
- August 2024 (12)
- July 2024 (11)
- June 2024 (9)
- May 2024 (13)
- April 2024 (12)
- March 2024 (12)
- February 2024 (12)
- January 2024 (10)
- 2023
- December 2023 (8)
- November 2023 (12)
- October 2023 (11)
- September 2023 (11)
- August 2023 (12)
- July 2023 (9)
- June 2023 (11)
- May 2023 (12)
- April 2023 (11)
- March 2023 (12)
- February 2023 (10)
- January 2023 (11)
- 2022
- December 2022 (11)
- November 2022 (12)
- October 2022 (11)
- September 2022 (13)
- August 2022 (11)
- July 2022 (10)
- June 2022 (13)
- May 2022 (11)
- April 2022 (12)
- March 2022 (10)
- February 2022 (11)
- January 2022 (13)
- 2021
- December 2021 (13)
- November 2021 (11)
- October 2021 (13)
- September 2021 (14)
- August 2021 (12)
- July 2021 (15)
- June 2021 (17)
- May 2021 (14)
- April 2021 (14)
- March 2021 (20)
- February 2021 (14)
- January 2021 (14)
- 2020
- December 2020 (13)
- November 2020 (17)
- October 2020 (12)
- September 2020 (14)
- August 2020 (11)
- July 2020 (18)
- June 2020 (16)
- May 2020 (14)
- April 2020 (20)
- March 2020 (12)
- February 2020 (13)
- January 2020 (14)
- 2019
- December 2019 (13)
- November 2019 (19)
- October 2019 (25)
- September 2019 (20)
- August 2019 (22)
- July 2019 (23)
- June 2019 (20)
- May 2019 (19)
- April 2019 (20)
- March 2019 (20)
- February 2019 (18)
- January 2019 (18)
- 2018
- December 2018 (19)
- November 2018 (19)
- October 2018 (17)
- September 2018 (16)
- August 2018 (21)
- July 2018 (20)
- June 2018 (21)
- May 2018 (17)
- April 2018 (19)
- March 2018 (21)
- February 2018 (15)
- January 2018 (20)
- 2017
- December 2017 (13)
- November 2017 (15)
- October 2017 (19)
- September 2017 (20)
- August 2017 (20)
- July 2017 (18)
- June 2017 (19)
- May 2017 (19)
- April 2017 (13)
- March 2017 (18)
- February 2017 (10)
- January 2017 (11)
- 2016
- December 2016 (9)
- November 2016 (14)
- October 2016 (21)
- September 2016 (10)
- August 2016 (11)
- July 2016 (8)
- June 2016 (10)
- May 2016 (5)
- April 2016 (11)
- March 2016 (12)
- February 2016 (11)
- January 2016 (8)
- 2015
- December 2015 (9)
- November 2015 (7)
- October 2015 (8)
- September 2015 (7)
- August 2015 (11)
- July 2015 (7)
- June 2015 (5)
- May 2015 (7)
- April 2015 (8)
- March 2015 (8)
- February 2015 (9)
- January 2015 (10)
- 2014
- December 2014 (12)
- November 2014 (7)
- October 2014 (11)
- September 2014 (10)
- August 2014 (9)
- July 2014 (12)
- June 2014 (9)
- May 2014 (12)
- April 2014 (9)
- March 2014 (6)
- February 2014 (1)
- January 2014 (26)