Corrosion Protection To Structural Part Interiors
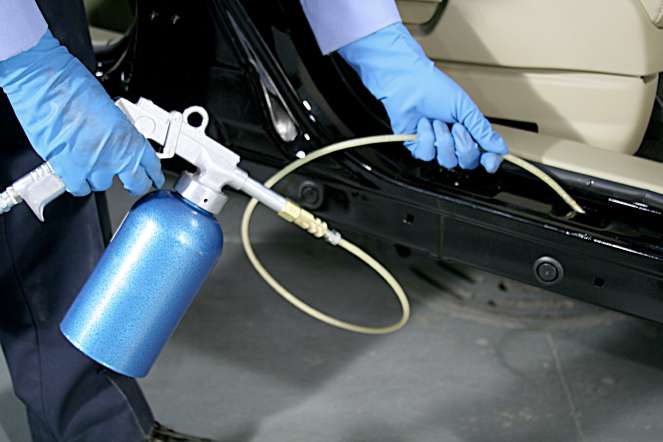
There has been a longstanding recommendation to apply epoxy primer, as well as anti-corrosion compound, on the inside of rails and pillars and rocker panels as a last step for structural repairs. Going back as far as the July/August 1988 I-CAR Advantage, in the article "Restoring Corrosion Protection," is the following step for providing corrosion protection to enclosed interior surfaces: "Apply primer. Two-part epoxy recommended. Then apply anti-corrosion compound." The reason given, is that on areas where the coatings have been entirely removed, this is a two-step process that is replacing the two original coatings, zinc and E-coat.
When researching for the recently updated I-CAR corrosion protection course, I-CAR asked several product and vehicle makers if this is still the most frequent recommendation. I-CAR was told it is not, due to several reasons. These include possible primer adhesion problems on these surfaces, the lower prevalence of epoxy primer at repair facilities, the increased popularity of self-etching primer, changing primer chemistries, and an increase in the effectiveness of anti-corrosion compound. E-coat is the best corrosion protection material that will ever be applied to a vehicle surface, and aside from the weld backside, the enclosed interior areas have E-coat.
Still, there is a concern among repair facilities for longevity of repairs, retaining corrosion warranties, and assurance that there is one more layer of protection, especially in the rust-belt areas. For these reasons, and more, several facilities will continue to apply epoxy primer in addition to anti-corrosion compound to enclosed surfaces as a standard operating procedure.
Primer Requires a Cleaned Surface
Product makers have a concern with adhesion if these backside areas are not cleaned properly. Any surface to be primed must be cleaned, both mechanically and chemically. If applying epoxy primer inside rails and other structural parts, the surfaces must be cleaned before the part is assembled. This requires sanding followed by a thorough chemical cleaning, especially the joint area backside to remove coatings. There might be access to a rail joint, if the joint is near the very tip of the rail and the rail is open-ended up through the joint location. Other than a situation like that, there isn't enough access for proper cleaning after welding, so it must be cleaned before assembly.
Anti-Corrosion Compound Alone
The recommendation from the product makers and vehicle makers that I-CAR communicated with during research for updating the I-CAR corrosion protection course is to apply anti-corrosion compound alone. Anti-corrosion compound, applied as a mist coat using a wand inserted through access holes or from the end of a rail, is designed to protect enclosed areas from corrosion (see Figure 1). The proper application technique should treat the backsides of the welds. Excess material should creep into the flange areas, sealing off those areas from moisture. At least one vehicle maker, Chrysler LLC (aka FCA/Stellantis), recommends a double application of anti-corrosion compound (see Video).
Video: Chrysler Collision Repair Manager Doug Craig explains that Chrysler recommends applying two coats of anti-corrosion compound.
Do Not Use Self-Etching Primer
It is still recommended to not use self-etching primer inside enclosed areas, because it doesn't form a barrier like epoxy primer and would eventually break down. Self-etching primer must be coated with another product, and it would be difficult to see inside an enclosed area whether or not the primer is completely coated by the anti-corrosion compound.
Conclusion
The recommendation to apply epoxy primer followed by anti-corrosion compound inside an enclosed area is not included in the updated I-CAR corrosion protection course. When using this two-step process, the surfaces must be cleaned for the primer to properly adhere. The more general recommendation is applying anti-corrosion compound alone.
This article first appeared in the August 4, 2011 edition of the I-CAR Advantage Online.
Related I-CAR Courses
-
Toyota/Lexus/Scion Position Statement: Pre- and Post-Repair System Scanning
Thursday, 28 July 2016
As the industry continues to ask if pre- and post-repair system scanning is necessary, Toyota/Lexus/Scion provides their answer.
-
Pre- and Post-Repair System Scanning Statements
Wednesday, 9 January 2019
Are you wondering if a particular OEM or organization has a published statement on pre-repair and post-repair scanning? We have compiled a list of most of the statements on the subject, so you can...
-
ADAS, Calibration, And Scanning Article Hotspot
Monday, 14 January 2019
Since advanced driver assistance systems (ADAS), scanning, and calibration first started becoming relevant, members of the collision repair industry have required as much knowledge as possible on...
-
Honda/Acura Position Statement: Pre- and Post-Repair System Scanning - UPDATE
Wednesday, 22 May 2019
Honda /Acura has updated their position statement on pre- and post-repair scanning to give more clarification on what is expected for scanning.
-
BMW Position Statement: Pre- and Post-Repair System Scanning - UPDATE
Friday, 10 April 2020
BMW has released a position statement related to pre- and post-repair system scanning. The statement applies to All vehicles equipped with on board diagnostics II (OBD II).
-
Quickly Identifying Outer Quarter Panels w/Rolled Hem Flanges
Monday, 5 March 2018
The I-CAR best practice article, Recycled Outer Quarter Panels w/Rolled Hem Flanges has gotten a lot of interest from the collision repair industry. It’s important to know which vehicles are...
-
General Motors Position Statement: Pre- and Post-Repair System Scanning
Friday, 21 October 2016
As the industry continues to ask, are pre- and post-repair scans necessary, General Motors provides their answer.
-
Restraints Wiring Repairs
Monday, 23 May 2016
Over the past few months, we've been sharing OEM position statements on restraints wiring repairs. Now we're bringing them all together in one place for easy reference.
-
FCA/Stellantis Position Statement: Pre- and Post-Repair System Scanning
Thursday, 9 June 2016
FCA/Stellantis has released a position statement related to pre- and post-repair system scanning.
-
Nissan/INFINITI Position Statement: Pre- and Post-Repair System Scanning - UPDATE
Monday, 14 January 2019
Nissan/INFINITI updated their position statement on pre- and post-repair scanning. The revised position statement touches on more subjects and gives additional information on the subject.
-
Repairer Driven News: Rivian Updates Door Handle Procedure
Sunday, 4 February 2035
Repairer Driven News (RDN) released an article featuring an updated Rivian procedure.
-
Audi Restraints Wiring: UPDATE
Friday, 5 September 2025
The question is often asked, "Can supplemental restraints system wiring be repaired?" The answer is: it depends on the vehicle maker. Let's take a look at Audi's position on this subject.
-
Repairers Realm: GMA Welding Machine Technology, Setup, And Maintenance - Now Available
Tuesday, 2 September 2025
I-CAR had a discussion on GMA welding machine technology, setup, and maintenance.
-
Ford And Lincoln Restraints Wiring: UPDATE
Friday, 29 August 2025
The question is often asked, "Can supplemental restraints system wiring be repaired?" The answer is: it depends on the vehicle maker. Let's take a look at Ford's and Lincoln's position on this...
-
High-Voltage Vehicle Research Tips: GM BEV Low-Voltage Battery Disconnection
Thursday, 28 August 2025
While researching OEM repair information, you may come across specific notes, instructions, or warnings for high-voltage (HV) vehicles. Some general procedures can be easily overlooked, so it’s...
-
High-Voltage Vehicle Research Tips
Thursday, 28 August 2025
While researching OEM repair information, you may come across specific notes, instructions, or warnings for high-voltage (HV) vehicles. Some general procedures can be easily overlooked, so it’s...
-
GM Part Replacement Without A Procedure
Friday, 22 August 2025
We are often asked, “What do I do if there isn’t a procedure to replace a service part?” Let’s see what GM says.
-
App-Based Connected Services Considerations: Ford/Lincoln
Tuesday, 19 August 2025
Have you had the experience where the vehicle notified the owner that it was being moved while it was in your repair facility? App-based connected services are available from many vehicle makers and may...
-
Digital Key Considerations: Ford/Lincoln
Tuesday, 19 August 2025
The intermingling of technology and automobiles continues, with digital key offerings from most vehicle makers. Digital keys utilize smartphone technology to expand vehicle access and owner...
-
Volkswagen Restraints Wiring: UPDATE
Thursday, 14 August 2025
The question is often asked, "Can supplemental restraints system wiring be repaired?" The answer is: it depends on the vehicle maker. Let's take a look at Volkswagen's position on this subject.
- 2025
- September 2025 (2)
- August 2025 (12)
- July 2025 (11)
- June 2025 (11)
- May 2025 (11)
- April 2025 (13)
- March 2025 (11)
- February 2025 (11)
- January 2025 (12)
- 2024
- December 2024 (8)
- November 2024 (11)
- October 2024 (13)
- September 2024 (10)
- August 2024 (12)
- July 2024 (11)
- June 2024 (9)
- May 2024 (13)
- April 2024 (12)
- March 2024 (12)
- February 2024 (12)
- January 2024 (10)
- 2023
- December 2023 (8)
- November 2023 (12)
- October 2023 (11)
- September 2023 (11)
- August 2023 (12)
- July 2023 (9)
- June 2023 (11)
- May 2023 (12)
- April 2023 (11)
- March 2023 (12)
- February 2023 (10)
- January 2023 (11)
- 2022
- December 2022 (11)
- November 2022 (12)
- October 2022 (11)
- September 2022 (13)
- August 2022 (11)
- July 2022 (10)
- June 2022 (13)
- May 2022 (11)
- April 2022 (12)
- March 2022 (10)
- February 2022 (11)
- January 2022 (13)
- 2021
- December 2021 (13)
- November 2021 (11)
- October 2021 (13)
- September 2021 (14)
- August 2021 (12)
- July 2021 (15)
- June 2021 (17)
- May 2021 (14)
- April 2021 (14)
- March 2021 (20)
- February 2021 (14)
- January 2021 (14)
- 2020
- December 2020 (13)
- November 2020 (17)
- October 2020 (12)
- September 2020 (14)
- August 2020 (11)
- July 2020 (18)
- June 2020 (16)
- May 2020 (14)
- April 2020 (20)
- March 2020 (12)
- February 2020 (13)
- January 2020 (14)
- 2019
- December 2019 (13)
- November 2019 (19)
- October 2019 (25)
- September 2019 (20)
- August 2019 (22)
- July 2019 (23)
- June 2019 (20)
- May 2019 (19)
- April 2019 (20)
- March 2019 (20)
- February 2019 (18)
- January 2019 (18)
- 2018
- December 2018 (19)
- November 2018 (19)
- October 2018 (17)
- September 2018 (16)
- August 2018 (21)
- July 2018 (20)
- June 2018 (21)
- May 2018 (17)
- April 2018 (19)
- March 2018 (21)
- February 2018 (15)
- January 2018 (20)
- 2017
- December 2017 (13)
- November 2017 (15)
- October 2017 (19)
- September 2017 (20)
- August 2017 (20)
- July 2017 (18)
- June 2017 (19)
- May 2017 (19)
- April 2017 (13)
- March 2017 (18)
- February 2017 (10)
- January 2017 (11)
- 2016
- December 2016 (9)
- November 2016 (14)
- October 2016 (21)
- September 2016 (10)
- August 2016 (11)
- July 2016 (8)
- June 2016 (10)
- May 2016 (5)
- April 2016 (11)
- March 2016 (12)
- February 2016 (10)
- January 2016 (8)
- 2015
- December 2015 (9)
- November 2015 (7)
- October 2015 (8)
- September 2015 (7)
- August 2015 (11)
- July 2015 (7)
- June 2015 (5)
- May 2015 (7)
- April 2015 (8)
- March 2015 (8)
- February 2015 (9)
- January 2015 (10)
- 2014
- December 2014 (12)
- November 2014 (7)
- October 2014 (11)
- September 2014 (10)
- August 2014 (9)
- July 2014 (12)
- June 2014 (9)
- May 2014 (12)
- April 2014 (9)
- March 2014 (6)
- February 2014 (1)
- January 2014 (26)