Thin-Film Technology Comes To Collision Repair
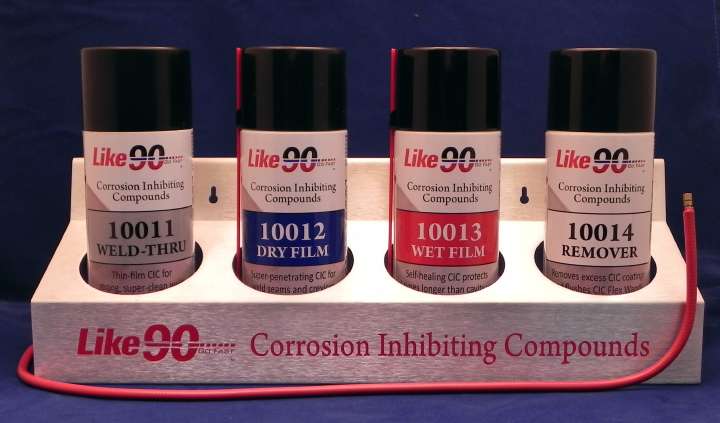
If you were asked for a short description for anti-corrosion compound, the material that is sprayed onto the backside of panels and inside rails after repairs, it is likely that "thin film" and "fine mist" would not be included in the wording. However, that is exactly the description given to a new type of anti-corrosion compound now available that uses what is collectively called thin-film technology.
Thin-film technology products are polymer resin-based, anything more descriptive than that is proprietary. They're a completely aerosol system being distributed by at least two product makers, Bonding Solutions with their Like90 Corrosion Protection System, and Sherwin Williams with their Shield Corrosion Protection System (see Figure 1). The two systems actually come from the same source that has its origins in the aerospace industry. The same material that's being recommended for spraying inside rails and panel cavities has been used for years on aluminum welds and sealing joints on aircraft. Besides an anti-corrosion compound, the line also includes a weld-through primer, also polymer resin-based, and a solvent-based cleaner.
Thin-Film Anti-Corrosion Compound
Figure 2 - The dedicated spray wand for the anti-corrosion compound is stiff, but flexible to allow a 360° spray pattern to reach all areas of a cavity.Most anti-corrosion compounds are wax-based, and even though applied as a fog spray, can quickly build up a heavy coating with the consistency of honey. The thin-film technology products start out thin, and the resulting coating is thin. This allows the material to not only coat the interior surfaces, but also wick out between the welded flanges from the inside. There is a dedicated wand that fits onto the aerosol spray can nozzle with a 360° fan pattern tip on the other end (see Figure 2). Like other anti-corrosion compound systems, the wand is for inserting into existing holes or into rails to apply the material onto areas that cannot be easily reached.
The thin-film nature of the material, combined with its creeping capability, allows applying it to joint edges after welding. On panel applications where there are no cavities, such as a welded radiator core support, the same cavity compound can be applied to the outside of the joints (see Figure 3). Just like it does from the inside, the thin film penetrates between the flanges from the outside, wicking around the welds to replace the weld-through primer that burned away. Excess material is cleaned off with the solvent-based remover, since it is not a good base for painting.
Figure 3 - On welded joints, the anti-corrosion compound can be sprayed on the outside of the joint after welding to allow it to wick into the joint.
There are two anti-corrosion compounds in each system. With the Shield system, there is a clear and a black compound, both identical except for the color. With the Like90 system, there's a dry film compound for sealing the joints after welding. The compound for cavity protection is a wet film that's self healing, similar to conventional anti-corrosion compounds.
Product specialists say it's perfectly OK to apply more coats of the cavity compound inside cavities, and even apply another brand of conventional wax-based anti-corrosion compound over the thin-film technology product, but it's not necessary.
Weldable Weld-Through Primer
The thin-film technology weld-through primer differs from other weld-through primers available in that it is not zinc- or copper-based, so it's not conductive. This allows the thin-film technology weld-through primer to be welded through. Our experience showed no problems with porosity when welding GMA plug welds without cleaning the material.
The instructions say to apply a very light coating on both mating surfaces and wait ten minutes before welding. The primer is still tacky at that point. Any weld-through primer on surfaces that will be refinished is cleaned off with the solvent remover.
Future Collision Repair Applications
Thin-film technology is also being considered for spraybooth masking and liquid masking applications. Liquid masking was actually the first collision repair application for the technology some years ago. The new plans are to improve that product. The product makers are also showcasing the benefits of thin-film technology to vehicle makers, though there are no specific recommendations or endorsements as of yet.
Conclusion
Thin-film technology products are one of the new offerings for automotive corrosion protection. The polymer resin-based aerosols are being offered as a thin anti-corrosion compound and weld-through primer with some unique qualities.
This article first appeared in the April 28, 2011 edition of the I-CAR Advantage Online.
Related I-CAR Courses
-
Toyota/Lexus/Scion Position Statement: Pre- and Post-Repair System Scanning
Thursday, 28 July 2016
As the industry continues to ask if pre- and post-repair system scanning is necessary, Toyota/Lexus/Scion provides their answer.
-
Pre- and Post-Repair System Scanning Statements
Wednesday, 9 January 2019
Are you wondering if a particular OEM or organization has a published statement on pre-repair and post-repair scanning? We have compiled a list of most of the statements on the subject, so you can...
-
ADAS, Calibration, And Scanning Article Hotspot
Monday, 14 January 2019
Since advanced driver assistance systems (ADAS), scanning, and calibration first started becoming relevant, members of the collision repair industry have required as much knowledge as possible on...
-
Honda/Acura Position Statement: Pre- and Post-Repair System Scanning - UPDATE
Wednesday, 22 May 2019
Honda /Acura has updated their position statement on pre- and post-repair scanning to give more clarification on what is expected for scanning.
-
BMW Position Statement: Pre- and Post-Repair System Scanning - UPDATE
Friday, 10 April 2020
BMW has released a position statement related to pre- and post-repair system scanning. The statement applies to All vehicles equipped with on board diagnostics II (OBD II).
-
Quickly Identifying Outer Quarter Panels w/Rolled Hem Flanges
Monday, 5 March 2018
The I-CAR best practice article, Recycled Outer Quarter Panels w/Rolled Hem Flanges has gotten a lot of interest from the collision repair industry. It’s important to know which vehicles are...
-
General Motors Position Statement: Pre- and Post-Repair System Scanning
Friday, 21 October 2016
As the industry continues to ask, are pre- and post-repair scans necessary, General Motors provides their answer.
-
Restraints Wiring Repairs
Monday, 23 May 2016
Over the past few months, we've been sharing OEM position statements on restraints wiring repairs. Now we're bringing them all together in one place for easy reference.
-
FCA/Stellantis Position Statement: Pre- and Post-Repair System Scanning
Thursday, 9 June 2016
FCA/Stellantis has released a position statement related to pre- and post-repair system scanning.
-
Nissan/INFINITI Position Statement: Pre- and Post-Repair System Scanning - UPDATE
Monday, 14 January 2019
Nissan/INFINITI updated their position statement on pre- and post-repair scanning. The revised position statement touches on more subjects and gives additional information on the subject.
-
Repairer Driven News: Rivian Updates Door Handle Procedure
Sunday, 4 February 2035
Repairer Driven News (RDN) released an article featuring an updated Rivian procedure.
-
GM Part Replacement Without A Procedure
Friday, 22 August 2025
We are often asked, “What do I do if there isn’t a procedure to replace a service part?” Let’s see what GM says.
-
App-Based Connected Services Considerations: Ford/Lincoln
Tuesday, 19 August 2025
Have you had the experience where the vehicle notified the owner that it was being moved while it was in your repair facility? App-based connected services are available from many vehicle makers and may...
-
Digital Key Considerations: Ford/Lincoln
Tuesday, 19 August 2025
The intermingling of technology and automobiles continues, with digital key offerings from most vehicle makers. Digital keys utilize smartphone technology to expand vehicle access and owner...
-
Volkswagen Restraints Wiring - UPDATE
Thursday, 14 August 2025
The question is often asked, "Can supplemental restraints system wiring be repaired?" The answer is: it depends on the vehicle maker. Let's take a look at Volkswagen's position on this subject.
-
Jaguar Land Rover Restraints Wiring - UPDATE
Thursday, 14 August 2025
The question is often asked, "Can supplemental restraints system wiring be repaired?" The answer is: it depends on the vehicle maker. Let's take a look at Jaguar Land Rover's position on this subject.
-
I-CAR Repairers Realm: GMA Welding Machine Technology, Setup, And Maintenance - Coming Soon
Wednesday, 13 August 2025
I-CAR is having a discussion on GMA Welding Machine Technology, Setup, And Maintenance.
-
Great Designs In Steel 2025 Presentations: A Closer Look At The VW ID.Buzz Body-In-White Construction
Friday, 8 August 2025
In case you missed it, Eike Schuppert presented the VW ID.Buzz Body-In-White Construction at Great Designs in Steel 2025.
-
Backup Battery And Low-Voltage Disconnect
Wednesday, 6 August 2025
When an accident happens, how will you call for help? Maybe the telematics system, equipped with a backup battery, could automatically do this, even if the main power is cut off. What are the repair...
-
Backup Battery And Low Voltage Disconnect: Kia
Wednesday, 6 August 2025
When an accident happens, how will you call for help? Maybe the telematics system, equipped with a backup battery, could automatically do this, even if the main power is cut off. What are the repair...
- 2025
- August 2025 (10)
- July 2025 (11)
- June 2025 (11)
- May 2025 (11)
- April 2025 (13)
- March 2025 (11)
- February 2025 (11)
- January 2025 (12)
- 2024
- December 2024 (8)
- November 2024 (11)
- October 2024 (13)
- September 2024 (10)
- August 2024 (12)
- July 2024 (11)
- June 2024 (9)
- May 2024 (13)
- April 2024 (12)
- March 2024 (12)
- February 2024 (12)
- January 2024 (10)
- 2023
- December 2023 (8)
- November 2023 (12)
- October 2023 (11)
- September 2023 (11)
- August 2023 (12)
- July 2023 (9)
- June 2023 (11)
- May 2023 (12)
- April 2023 (11)
- March 2023 (12)
- February 2023 (10)
- January 2023 (11)
- 2022
- December 2022 (11)
- November 2022 (12)
- October 2022 (11)
- September 2022 (13)
- August 2022 (11)
- July 2022 (10)
- June 2022 (13)
- May 2022 (11)
- April 2022 (12)
- March 2022 (10)
- February 2022 (11)
- January 2022 (13)
- 2021
- December 2021 (13)
- November 2021 (11)
- October 2021 (13)
- September 2021 (14)
- August 2021 (12)
- July 2021 (15)
- June 2021 (17)
- May 2021 (14)
- April 2021 (14)
- March 2021 (20)
- February 2021 (14)
- January 2021 (14)
- 2020
- December 2020 (13)
- November 2020 (17)
- October 2020 (12)
- September 2020 (14)
- August 2020 (11)
- July 2020 (18)
- June 2020 (16)
- May 2020 (14)
- April 2020 (20)
- March 2020 (12)
- February 2020 (13)
- January 2020 (14)
- 2019
- December 2019 (13)
- November 2019 (19)
- October 2019 (25)
- September 2019 (20)
- August 2019 (22)
- July 2019 (23)
- June 2019 (20)
- May 2019 (19)
- April 2019 (20)
- March 2019 (20)
- February 2019 (18)
- January 2019 (18)
- 2018
- December 2018 (19)
- November 2018 (19)
- October 2018 (17)
- September 2018 (16)
- August 2018 (21)
- July 2018 (20)
- June 2018 (21)
- May 2018 (17)
- April 2018 (19)
- March 2018 (21)
- February 2018 (15)
- January 2018 (20)
- 2017
- December 2017 (13)
- November 2017 (15)
- October 2017 (19)
- September 2017 (20)
- August 2017 (20)
- July 2017 (18)
- June 2017 (19)
- May 2017 (19)
- April 2017 (13)
- March 2017 (18)
- February 2017 (10)
- January 2017 (11)
- 2016
- December 2016 (9)
- November 2016 (14)
- October 2016 (21)
- September 2016 (10)
- August 2016 (11)
- July 2016 (8)
- June 2016 (10)
- May 2016 (6)
- April 2016 (11)
- March 2016 (12)
- February 2016 (11)
- January 2016 (8)
- 2015
- December 2015 (9)
- November 2015 (7)
- October 2015 (8)
- September 2015 (7)
- August 2015 (11)
- July 2015 (7)
- June 2015 (5)
- May 2015 (7)
- April 2015 (8)
- March 2015 (8)
- February 2015 (9)
- January 2015 (10)
- 2014
- December 2014 (12)
- November 2014 (7)
- October 2014 (11)
- September 2014 (10)
- August 2014 (9)
- July 2014 (12)
- June 2014 (9)
- May 2014 (12)
- April 2014 (9)
- March 2014 (6)
- February 2014 (1)
- January 2014 (26)