Today’s Advanced Vehicles Require Changes in Collision Repair Attachment Methods - Part 1
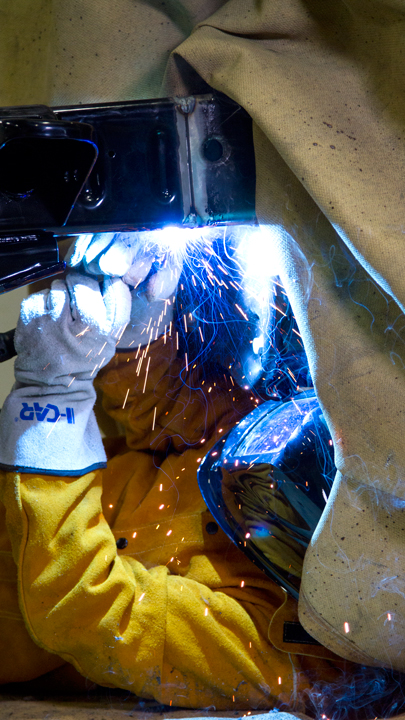
This article originally appeared in the November/December edition of Fixed Ops Magazine.
Collision repair professionals are no different than any other professional – we are resistant to change. It took many years for repairers to make the switch to “MIG welding” for welding early unibody vehicles. (For this article we’ll use the term gas metal arc welding (GMAW) metal inert gas (MIG), or GMA (MIG)). (More on the reason, later.) It was a technology that was unfamiliar to many and there wasn’t a perceived need for change. History would prove otherwise, as there may not be a collision repair business in the country that doesn’t have a GMA (MIG) welder.
In this first of a two-part series, we’ll take a look at some of the attachment methods required for today’s collision-damaged vehicles. We will focus on steel and aluminum welding. In part 2, we’ll take a closer look at adhesive bonding and some of the mechanical fasteners that are going to be required for repair.
Steel GMA (MIG) Welding
GMA (MIG) welding has been a staple in the collision repair industry for many years. Steel GMA (MIG) welders offer collision repair professionals a number of benefits: modest price to own; ease of use; readily available training; minimal maintenance; and technicians are familiar with the equipment.
When steel GMA (MIG) welding started its rise, it was often referred to simply as MIG welding. While this term is widely known, it’s not really accurate. MIG stands for “metal inert gas” and is accurate when making welds using an inert shielding gas, such as 100 percent argon. However, for most collision repairs, we use a shielding gas that is 75 percent argon, 25 percent carbon dioxide (often called 75/25, or C-25). Because carbon dioxide is an active gas, the correct term would be MAG welding. Regardless, if a technician is doing MIG welding, or MAG welding, both processes are gas metal arc (GMA) welding methods, so I CAR, the Inter-Industry Conference on Auto Collision Repair, and others, made the switch to GMA (MIG) when referring to the process - GMA, to be technically accurate, and MIG to help with its recognize-ability…simple enough, right?
Because steel GMA (MIG) welding has been prevalent in the collision repair industry for so long, we won’t spend a lot of time on it in this article. However, there are a few important items that we do need to touch on. For the majority of unibody welding, we will likely be using a 110V machine, with 0.6–0.9 mm (.023–.035") ER70S 6 electrode wire, and C-25 shielding gas. For welding on truck frames, we may still be using ER70S-6 electrode wire, with C-25 shielding gas, but we’ll need a 220 V machine and 1.2 mm (.045") electrode wire. Also, be aware that some vehicle makers do require ER70S 3 electrode wire for some welding applications. As always, it’s important to refer to the vehicle maker’s instructions for any part replacement and welding requirements.
A recent example of a new vehicle maker requirement for welding is the announcement by Honda that ER70S-6 wire only be used on steels with a tensile strength of 440 MPa or less. For any steel on Honda vehicles between 440 MPa and 980 MPa, Honda now requires Bosch’s DS980J electrode wire. I-CAR, through the I-CAR Repairability Technical Support Portal, has a copy of the requirement from a recent Honda Body Repair News publication. You can access the publication, along with a lot of other great vehicle maker information at www.rts.i-car.com, or you can go directly to the article at Honda Body Repair Manual Welding & Sectioning Guideline Revisions
Aluminum GMA (MIG) Welding
A lot of people tell us that aluminum repair isn’t difficult, it’s just different; but when it comes to welding, it’s a lot different. Unlike steel GMA (MIG) welding, aluminum welding is truly MIG welding. Because 100 percent argon shielding gas is used, the “inert” moniker is completely accurate for aluminum welding. There are also a number of other differences between steel and aluminum welding. (Image #5610)
While steel welding affords technicians with the option of either the push or pull welding technique, the push technique must be used for aluminum. The push technique allows for the shielding gas to clean the weld area and reduce weld contamination.
The welding transfer method also differs between steel and aluminum welding. For steel, short-circuit transfer is still the transfer methods of choice. However, for aluminum, most vehicle makers are now requiring pulsed-spray arc transfer. Unlike short-circuit transfer, where molten electrode wire "breaks off" when it contacts the base metal, pulsed spray forms a droplet of molten electrode wire that is pushed across the arc into the weld puddle. Because the concept is easier to show, than explain, check out these slow motion videos from Miller Electric, for a comparison of the two transfer methods:
Another difference between steel and aluminum welding is electrode wire selection. While there is a nearly universal electrode type for steel, aluminum electrode requirements vary, based on the alloy of the base metal and the vehicle maker’s recommendation. It’s imperative to refer to the vehicle maker’s instructions when selecting aluminum electrode wires. Some common types you may run into include 4043, 4047, 5356, and 5554.
Squeeze-Type Resistance Spot Welding (STRSW)
Not since GMA (MIG) welding first made its way into collision repair facilities across the country, has there been a repair attachment method gaining popularity as much as spot welding. A quality squeeze-type resistance spot welder has become an essential piece of equipment for collision repair businesses.
Not only does STRSW duplicate the OEM appearance, but it also allows for a significantly smaller heat-affected zone that doesn’t damage many of the high- (HSS) and ultra-high strength steels (UHSS) found on today’s vehicles. Some vehicle makers have gone as far as requiring STRSW for welding HSS and UHSS on their late-model vehicles.
In the July/August edition of (Fixed Ops Magazine) we took a closer look at some of the considerations for investing in this type of equipment. If you haven’t already done so, it’s time to take a closer look at making an investment into this type of equipment; you’ll be glad you did. We also covered MIG brazing in the previous article and you may also want to consider adding this piece of equipment into your facility.
Multi-Function Welders
One trend that we’re beginning to see from welding machine manufacturers is machines that integrate a number of welding processes into one machine. There are a handful of machines now on the market that you can make steel GMA (MIG) welds, MIG braze welds, and aluminum GMA (MIG) welds without making modifications to the machine each time you change welding processes.
These machines offer three welding torches and the ability to house three types of electrode wire, in the same welding machine. The machine can carry 100 percent argon shielding gas and C 25 shielding gas. You don’t even have to “tell” the machine which welding method you’d like to use. When you squeeze the trigger on the steel GMA (MIG) welding torch, the machine switches, automatically, to steel welding mode and provides C-25 shielding gas to the nozzle. Squeeze the trigger on the MIG brazing welding torch and, again, the machines switches automatically and sends 100 percent argon to the nozzle. Some of these machines even allow for conversion to Tungsten Inert Gas (TIG) welding and stick welding.
Stay Current with Tools, Equipment and Training
Automotive technology continues to evolve at a rapid pace. As technology evolves, collision repair processes will continue to evolve as well. It’s important to continuously refer to the vehicle maker recommendations for attachment methods. While steel GMA (MIG) welding will continue to be used for the foreseeable future, STRSW and MIG brazing will continue to rise in popularity and will be required for certain collision repairs.
As aluminum-intensive vehicle production increases, aluminum GMA (MIG) welding will also continue to rise. It’s important that you not resist change in order to keep up. You need to equip your facility with the proper tools and equipment to perform complete, safe, and quality repairs; and it’s imperative that your technicians have the most up-to-date training on how to leverage each of these technologies. I-CAR offers a number of courses on attachment methods. To see which classes are available in your area, visit www.i-car.com.
In addition to I-CAR training courses, the I-CAR Welding Training & Certification™ program includes instruction on welding theory, a hands-on evaluation by the Instructor of the facility’s gear, equipment, and infrastructure prior to the in-shop training, practice, and the industry-recognized certification test. More information on all of I-CAR’s welding courses (Steel GMA (MIG) Welding, Aluminum GMA (MIG) Welding, and Steel Sectioning) can be found at I-CAR Welding & Certification. Pricing for welding training has been reduced to make it more affordable for every technician to have the hands-on training needed to complete a proper weld. A growing number of OEMs use I-CAR Welding Training & Certification in their network programs, including Acura, Audi, Chrysler, Ford, GM, Honda, Infiniti, Jaguar, Land Rover, Lexus, Nissan, Porsche, Scion, Toyota, Volvo and Volkswagen.
In the next article, we’ll take an in-depth look at adhesive bonding, rivets and rivet bonding, and other mechanical fasteners.
Additional I-CAR Collision Repair News you may find helpful:
Related I-CAR Courses
-
Toyota/Lexus/Scion Position Statement: Pre- and Post-Repair System Scanning
Thursday, 28 July 2016
As the industry continues to ask if pre- and post-repair system scanning is necessary, Toyota/Lexus/Scion provides their answer.
-
Pre- and Post-Repair System Scanning Statements
Wednesday, 9 January 2019
Are you wondering if a particular OEM or organization has a published statement on pre-repair and post-repair scanning? We have compiled a list of most of the statements on the subject, so you can...
-
ADAS, Calibration, And Scanning Article Hotspot
Monday, 14 January 2019
Since advanced driver assistance systems (ADAS), scanning, and calibration first started becoming relevant, members of the collision repair industry have required as much knowledge as possible on...
-
Honda/Acura Position Statement: Pre- and Post-Repair System Scanning - UPDATE
Wednesday, 22 May 2019
Honda /Acura has updated their position statement on pre- and post-repair scanning to give more clarification on what is expected for scanning.
-
BMW Position Statement: Pre- and Post-Repair System Scanning - UPDATE
Friday, 10 April 2020
BMW has released a position statement related to pre- and post-repair system scanning. The statement applies to All vehicles equipped with on board diagnostics II (OBD II).
-
Quickly Identifying Outer Quarter Panels w/Rolled Hem Flanges
Monday, 5 March 2018
The I-CAR best practice article, Recycled Outer Quarter Panels w/Rolled Hem Flanges has gotten a lot of interest from the collision repair industry. It’s important to know which vehicles are...
-
General Motors Position Statement: Pre- and Post-Repair System Scanning
Friday, 21 October 2016
As the industry continues to ask, are pre- and post-repair scans necessary, General Motors provides their answer.
-
Restraints Wiring Repairs
Monday, 23 May 2016
Over the past few months, we've been sharing OEM position statements on restraints wiring repairs. Now we're bringing them all together in one place for easy reference.
-
FCA/Stellantis Position Statement: Pre- and Post-Repair System Scanning
Thursday, 9 June 2016
FCA/Stellantis has released a position statement related to pre- and post-repair system scanning.
-
Nissan/INFINITI Position Statement: Pre- and Post-Repair System Scanning - UPDATE
Monday, 14 January 2019
Nissan/INFINITI updated their position statement on pre- and post-repair scanning. The revised position statement touches on more subjects and gives additional information on the subject.
-
Repairer Driven News: Rivian Updates Door Handle Procedure
Sunday, 4 February 2035
Repairer Driven News (RDN) released an article featuring an updated Rivian procedure.
-
Audi Restraints Wiring: UPDATE
Friday, 5 September 2025
The question is often asked, "Can supplemental restraints system wiring be repaired?" The answer is: it depends on the vehicle maker. Let's take a look at Audi's position on this subject.
-
Repairers Realm: GMA Welding Machine Technology, Setup, And Maintenance - Now Available
Tuesday, 2 September 2025
I-CAR had a discussion on GMA welding machine technology, setup, and maintenance.
-
Ford And Lincoln Restraints Wiring: UPDATE
Friday, 29 August 2025
The question is often asked, "Can supplemental restraints system wiring be repaired?" The answer is: it depends on the vehicle maker. Let's take a look at Ford's and Lincoln's position on this...
-
High-Voltage Vehicle Research Tips: GM BEV Low-Voltage Battery Disconnection
Thursday, 28 August 2025
While researching OEM repair information, you may come across specific notes, instructions, or warnings for high-voltage (HV) vehicles. Some general procedures can be easily overlooked, so it’s...
-
High-Voltage Vehicle Research Tips
Thursday, 28 August 2025
While researching OEM repair information, you may come across specific notes, instructions, or warnings for high-voltage (HV) vehicles. Some general procedures can be easily overlooked, so it’s...
-
GM Part Replacement Without A Procedure
Friday, 22 August 2025
We are often asked, “What do I do if there isn’t a procedure to replace a service part?” Let’s see what GM says.
-
App-Based Connected Services Considerations: Ford/Lincoln
Tuesday, 19 August 2025
Have you had the experience where the vehicle notified the owner that it was being moved while it was in your repair facility? App-based connected services are available from many vehicle makers and may...
-
Digital Key Considerations: Ford/Lincoln
Tuesday, 19 August 2025
The intermingling of technology and automobiles continues, with digital key offerings from most vehicle makers. Digital keys utilize smartphone technology to expand vehicle access and owner...
-
Volkswagen Restraints Wiring: UPDATE
Thursday, 14 August 2025
The question is often asked, "Can supplemental restraints system wiring be repaired?" The answer is: it depends on the vehicle maker. Let's take a look at Volkswagen's position on this subject.
- 2025
- September 2025 (2)
- August 2025 (12)
- July 2025 (11)
- June 2025 (11)
- May 2025 (11)
- April 2025 (13)
- March 2025 (11)
- February 2025 (11)
- January 2025 (12)
- 2024
- December 2024 (8)
- November 2024 (11)
- October 2024 (13)
- September 2024 (10)
- August 2024 (12)
- July 2024 (11)
- June 2024 (9)
- May 2024 (13)
- April 2024 (12)
- March 2024 (12)
- February 2024 (12)
- January 2024 (10)
- 2023
- December 2023 (8)
- November 2023 (12)
- October 2023 (11)
- September 2023 (11)
- August 2023 (12)
- July 2023 (9)
- June 2023 (11)
- May 2023 (12)
- April 2023 (11)
- March 2023 (12)
- February 2023 (10)
- January 2023 (11)
- 2022
- December 2022 (11)
- November 2022 (12)
- October 2022 (11)
- September 2022 (13)
- August 2022 (11)
- July 2022 (10)
- June 2022 (13)
- May 2022 (11)
- April 2022 (12)
- March 2022 (10)
- February 2022 (11)
- January 2022 (13)
- 2021
- December 2021 (13)
- November 2021 (11)
- October 2021 (13)
- September 2021 (14)
- August 2021 (12)
- July 2021 (15)
- June 2021 (17)
- May 2021 (14)
- April 2021 (14)
- March 2021 (20)
- February 2021 (14)
- January 2021 (14)
- 2020
- December 2020 (13)
- November 2020 (17)
- October 2020 (12)
- September 2020 (14)
- August 2020 (11)
- July 2020 (18)
- June 2020 (16)
- May 2020 (14)
- April 2020 (20)
- March 2020 (12)
- February 2020 (13)
- January 2020 (14)
- 2019
- December 2019 (13)
- November 2019 (19)
- October 2019 (25)
- September 2019 (20)
- August 2019 (22)
- July 2019 (23)
- June 2019 (20)
- May 2019 (19)
- April 2019 (20)
- March 2019 (20)
- February 2019 (18)
- January 2019 (18)
- 2018
- December 2018 (19)
- November 2018 (19)
- October 2018 (17)
- September 2018 (16)
- August 2018 (21)
- July 2018 (20)
- June 2018 (21)
- May 2018 (17)
- April 2018 (19)
- March 2018 (21)
- February 2018 (15)
- January 2018 (20)
- 2017
- December 2017 (13)
- November 2017 (15)
- October 2017 (19)
- September 2017 (20)
- August 2017 (20)
- July 2017 (18)
- June 2017 (19)
- May 2017 (19)
- April 2017 (13)
- March 2017 (18)
- February 2017 (10)
- January 2017 (11)
- 2016
- December 2016 (9)
- November 2016 (14)
- October 2016 (21)
- September 2016 (10)
- August 2016 (11)
- July 2016 (8)
- June 2016 (10)
- May 2016 (5)
- April 2016 (11)
- March 2016 (12)
- February 2016 (10)
- January 2016 (8)
- 2015
- December 2015 (9)
- November 2015 (7)
- October 2015 (8)
- September 2015 (7)
- August 2015 (11)
- July 2015 (7)
- June 2015 (5)
- May 2015 (7)
- April 2015 (8)
- March 2015 (8)
- February 2015 (9)
- January 2015 (10)
- 2014
- December 2014 (12)
- November 2014 (7)
- October 2014 (11)
- September 2014 (10)
- August 2014 (9)
- July 2014 (12)
- June 2014 (9)
- May 2014 (12)
- April 2014 (9)
- March 2014 (6)
- February 2014 (1)
- January 2014 (26)