Advanced Driver Assistance Systems (ADAS) Collision Repair Diagnostics Process
Posted on 10 January 2017
| Share:
|
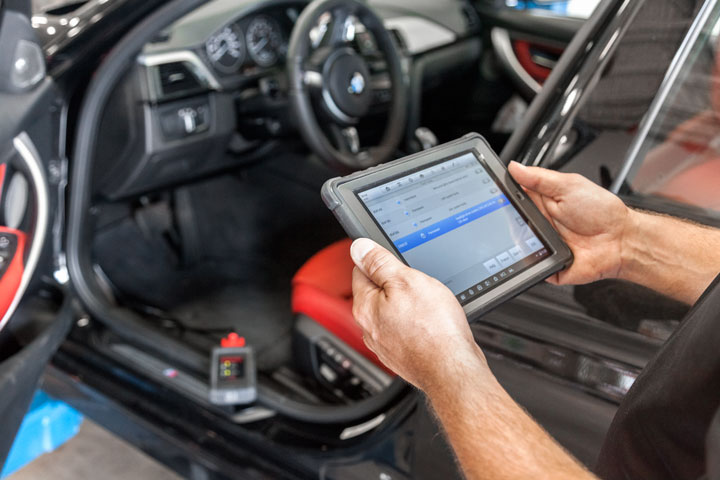
For the past several months, I-CAR and subject matter experts from vehicle makers, collision repairers, insurers, and tool and equipment makers have been meeting to develop, update, and publish an I-CAR best practice on Advanced driver Assistance Systems (ADAS) Collision Repair Diagnostic Processes.
This best practice is designed to be used in conjunction with the "I-CAR Best Practice: Collision Repair Diagnostics Definitions," published in October 2016.
Disclaimer
Before any repair decisions are made, access to OEM repair information is required. Diagnostic trouble codes (DTCs) do not identify which part needs to be replaced, rather DTCs are a piece of the diagnostic process that will lead a trained and qualified technician to the correct test to accurately diagnose the damage. Ensure that you have proper battery support when scanning. Although this process was developed to cover advanced driver assistance systems (ADAS), the process can be applied to other electronic systems, such as restraints, adaptive lighting, and other systems that may require calibration and/or aiming.
Pre-Repair Scan Process
- Conduct customer consultation.
- Gain customer authorization to scan vehicle and to share data with appropriate parties involved (Sublet Technician/Insurer/Repair Facility Personnel)
- Check for malfunction indicator lamps (MILs) and/or information display messages.
- The 12-volt electrical system must be enabled to identify any MILs.
- Not all systems will illuminate MILs, even if there is damage to that system.
- Document any MILs and/or information display messages.
- Identify advanced driver assistance systems (ADAS). (collision braking, lane keep assist, adaptive cruise control, etc.).
- Document ADAS.
- Document potential damage to ADAS, ADAS mounting location(s), damage that may affect ADAS, or parts that will need to be R&I near ADAS.
- Identify calibration/initialization/aiming requirements for ADAS parts, including required calibration/initialization following R&I.
- RTS - OEM Calibration Requirements Search
- OEM information
- Identify enable and disable switches
- Enablement/disablement may be required for some calibration procedures.
- If it is turned off, system may not be able to be calibrated.
- Systems that can be enabled/disabled should be documented, so that a system is not turned on when customer wants it off.
- Perform pre-repair scan.
- A pre-repair scan is not possible if the 12-volt electrical system and vehicle communication networks are disabled or cannot be maintained throughout the scan. If a pre-repair scan is not possible because of vehicle damage, it should be done as soon as repair progress allows it to be done safely.
- Document DTCs and other data.
- Does not include black box info, speed of accident/accident recreation
- Include pending, current, and past DTCs
- Access OEM information to identify system(s) affected by DTCs.
- Access to OEM information is required
- Check OEM information for bulletins/recalls/campaigns for DTCs
- Determine likely related and unrelated DTCs.
- Leverage the "Collision Advantage"
- Key cycles/time stamps/freeze-frame data
Post Repair Calibration(s) and Post Scan Processes
- Perform all required calibration/initialization/aiming steps, following OEM published procedures.
- Some systems will require the vehicle to be driven to perform calibration/initialization/aiming within the required driving parameters.
- Some systems will not detect issues within the system until the vehicle is driven within the required driving parameters.
- Some systems will require special tools and/or aiming equipment for calibration/initialization/aiming.
- Some systems will require both.
- Perform post-repair scan.
- If related DTCs return, begin OEM published diagnostic process to determine error.
Additional I-CAR Collision Repair News you may find helpful: