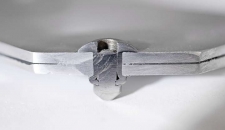
Dressing GMA Welds
- Posted on 03 April 2013
There's a lot of information in the field on making and testing GMA welds, but not too much on dressing the welds after they're made on a vehicle. Any GMA weld usually requires dressing the top surface of the weld.
Front Lower Rail Section With No Welding
- Posted on 27 February 2013
If there is a sectioning procedure on a front lower rail, GMA welding across a seam is the usual method for attaching the new joint. On at least two late model Porsche vehicles, however, there is a front lower rail sectioning procedure that uses no welds at all. The rails on the Panamera, since 2010, and the 911, since 2012, both have aluminum construction.
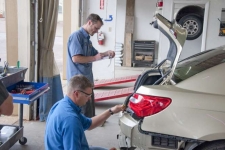
Necessary Culture Changes For The Blueprinting Process
- Posted on 03 December 2012
Blueprinting is a term often heard in the collision repair industry. Blueprinting means different things to different people, but blueprinting really is establishing a standard operating procedure (SOP) that allows for the discovery of all the damage before repairs begin. As part of the blueprinting process, all the parts should be identified right down to the blend panels and the clips that are needed. The correct repair information should be found along with any color matching that needs to be done. Following these steps and others, before repairs begin, will eliminate the problems that arise from finding additional damage during the repair process, which can interrupt and delay the repairs on that vehicle. Worse yet, is when the vehicle is repaired incorrectly because vehicle maker repair procedures were not followed.
One of the biggest challenges to implementing the blueprinting process may be the staff's perception of what will be involved. To be successful, those perceptions must be changed.
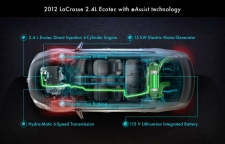
General Motors eAssist Electric System
- Posted on 11 October 2012
Another version of electric-assist vehicle technology is showing up in collision repair facilities. General Motors in 2012 introduced what it refers to as "light electrification" technology on select models. This system is called eAssist, and is available on some 2012 Buick LaCrosse, Regal, and 2013 Chevrolet Malibu models (see Figure 1).
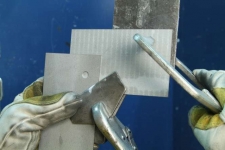
Revised I-CAR Training and Certification: Steel GMA Welding Course
- Posted on 22 August 2012
The challenges for vehicle makers to make vehicles safe and strong as well as lightweight have resulted in material variations. Many of today's steel-structured vehicles use steel in the range of 0.70 mm thickness for the outer panels, and a thicker, and in many cases higher strength, steel for the structure. This has resulted in I-CAR revising its Training and Certification: Steel GMA Welding to more accurately reflect the thicknesses of steels being used.
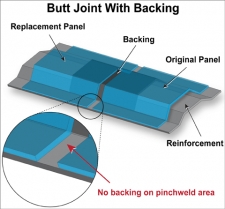
General Motors Overlap Sectioning Joint
- Posted on 31 May 2012
Until recently, General Motors has generally specified butt joints with backings when sectioning parts of a uniside. However, an overlap joint is now being required for some uniside sectioning joints. This is being done to reduce the transfer of heat from GMA welding into heat-sensitive high- and ultra-high-strength steel reinforcements. The concern with a butt joint with backing is that the backing piece does not extend to the pinchweld flange, and leaves the reinforcement exposed. As a result, a GMA weld is made on the pinchweld flange area of the reinforcement (see Figure 1).
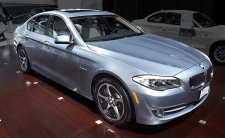
Bonding And Rivet Bonding Technology On Steel BMW Vehicle Parts
- Posted on 26 April 2012
As BMW Groups' vehicle construction technology advances, so does the repair process required to fix them properly. Conventional welding, which has been used primarily in BMW Groups' repair processes in the past, is slowly becoming the secondary method to bonding and rivet bonding technology. BMW currently recommends primarily using bonding and rivet bonding to replace exterior body panels, structural parts, and sectioning specific locations in conjunction with VIN-specific repair procedures. Changes in recommended repair procedures affect all current production models. This does not mean that all models, and all parts, are affected though. Consulting VIN-specific repair procedures should always be the first step in the repair process. The same is true for Mini and for Rolls-Royce vehicles (see Figure 1).
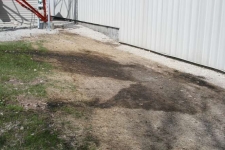
Oil Spill At The I-CAR Tech Center
- Posted on 06 March 2012
A small motor oil spill incident at the I-CAR Tech Center in Appleton, Wisconsin in the spring of 2011 has raised our awareness of the many considerations involved with a material spill into the environment. What started as an accidental collision between a snowplow and a 55-gallon drum of waste oil on an adjoining property resulted in an experience we would never want to repeat.
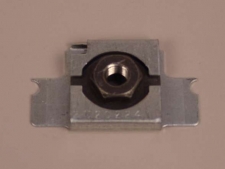
Ford F-150 Body Mount Cage Nuts
- Posted on 22 December 2011
Beginning with the 2009 model year Ford F-150, the cab body mount bolts are secured with a cage nut. The cage nut is held in position inside a cage nut retainer that is attached to the inside of a floor crossmember. The crossmember is attached to the underside of the floor pan, which creates an enclosure for the cage nut. The retainer has two nut retaining tabs, one on each opposing side of the nut that are folded against the nut to hold it in place (see Figure 1).
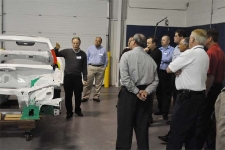
Don't Section Ultra-High-Strength Steel - I-CAR Repairability Summit Identifies Best Practices
- Posted on 10 October 2011
Unless specifically recommended by the vehicle maker, parts with a tensile strength over 600 MPa should only be replaced at factory seams. This is just one of the "best practices" identified at a Repairability Summit hosted by I-CAR. Summit attendees consisted of subject matter experts from vehicle makers, tool and equipment makers, collision repair facilities, insurance companies, and the American Iron and Steel Institute.
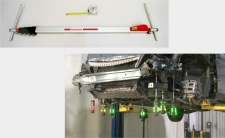
Three-Dimensional Measuring Equipment - Is It Really Necessary?
- Posted on 08 September 2011
I-CAR has been emphasizing the importance of three-dimensional measuring since its founding in 1979, but is it really required to repair a vehicle? After all, three-dimensional measuring systems are considerably more expensive compared to the much more affordable tape measure or tram gauge (see Figure 1).
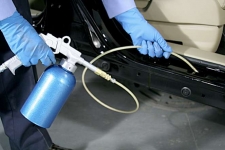
Corrosion Protection To Structural Part Interiors
- Posted on 04 August 2011
There has been a longstanding recommendation to apply epoxy primer, as well as anti-corrosion compound, on the inside of rails and pillars and rocker panels as a last step for structural repairs. Going back as far as the July/August 1988 I-CAR Advantage, in the article "Restoring Corrosion Protection," is the following step for providing corrosion protection to enclosed interior surfaces: "Apply primer. Two-part epoxy recommended. Then apply anti-corrosion compound." The reason given, is that on areas where the coatings have been entirely removed, this is a two-step process that is replacing the two original coatings, zinc and E-coat.
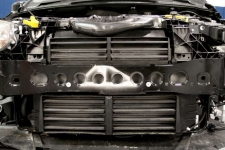
2012 Ford Focus Active Grille Shutters
- Posted on 29 June 2011
When making collision repairs to the 2012 Ford Focus, be aware that the vehicle may be equipped with an active grille shutter system (see Figure 1). This motorized system is located in front of the radiator, which places it in a vulnerable position during front-end collisions.
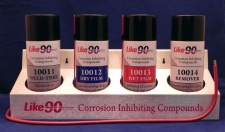
Thin-Film Technology Comes To Collision Repair
- Posted on 28 April 2011
If you were asked for a short description for anti-corrosion compound, the material that is sprayed onto the backside of panels and inside rails after repairs, it is likely that "thin film" and "fine mist" would not be included in the wording. However, that is exactly the description given to a new type of anti-corrosion compound now available that uses what is collectively called thin-film technology.
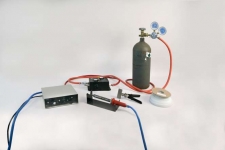
Nitrogen Hot Air Welding
- Posted on 30 March 2011
Hot air welders have been around for a number of years and used mostly in bumper remanufacturing facilities. A hot air welder works by passing compressed air over a heating element and heating the air to around 345°C (650°F) to melt the base plastic and filler rod/ribbon together. This type of welder does not use a flat shoe or feeder tube-type tip. A V-groove is cut into the part, the rod is laid into the V-groove, and the two are melted together. Whenever using this type of welder, it is important to have airflow over the element at all times no matter if it is preheating, welding, or cooling.
-
Toyota/Lexus/Scion Position Statement: Pre- and Post-Repair System Scanning
Thursday, 28 July 2016
As the industry continues to ask if pre- and post-repair system scanning is necessary, Toyota/Lexus/Scion provides their answer.
-
Pre- and Post-Repair System Scanning Position Statements
Wednesday, 9 January 2019
Are you wondering if a particular OEM or organization has a published position statement on pre-repair and post-repair scanning? We have compiled a list of most of the position statements on the...
-
ADAS, Calibration, And Scanning Article Hotspot
Monday, 14 January 2019
Since advanced driver assistance systems (ADAS), scanning, and calibration first started becoming relevant, members of the collision repair industry have required as much knowledge as possible on...
-
Honda/Acura Position Statement: Pre- and Post-Repair System Scanning - UPDATE
Wednesday, 22 May 2019
Honda /Acura has updated their position statement on pre- and post-repair scanning to give more clarification on what is expected for scanning.
-
Restraints Wiring Repairs
Monday, 23 May 2016
Over the past few months, we've been sharing OEM position statements on restraints wiring repairs. Now we're bringing them all together in one place for easy reference.
-
Typical Calibration Requirements For Blind Spot Sensors
Wednesday, 19 October 2016
Technicians should be aware of what’s required to keep advanced driver assistance systems (ADAS) running safely after a collision. Whether that be aiming a camera, which can cause a system to not...
-
Typical Calibration Requirements For Forward Radar Sensors
Wednesday, 12 October 2016
Technicians should be aware of what’s required to keep advanced driver assistance systems (ADAS) running safely after a collision. Whether that be aiming a camera, which can cause a system to not...
-
General Motors Position Statement: Pre- and Post-Repair System Scanning
Friday, 21 October 2016
As the industry continues to ask, are pre- and post-repair scans necessary, General Motors provides their answer.
-
FCA/Stellantis Position Statement: Pre- and Post-Repair System Scanning
Thursday, 9 June 2016
FCA/Stellantis has released a position statement related to pre- and post-repair system scanning.
-
Quickly Identifying Outer Quarter Panels w/Rolled Hem Flanges
Monday, 5 March 2018
The I-CAR best practice article, Recycled Outer Quarter Panels w/Rolled Hem Flanges has gotten a lot of interest from the collision repair industry. It’s important to know which vehicles are...
-
Calibration Research Tips: Nissan/INFINITI - Bumper Cover Replaced With Sonar Sensor Holder
Thursday, 9 May 2024
While searching for information on advanced driver assistance systems (ADAS) on an OEM repair information site, you may come across unique calibration procedures or events. These events can vary by...
-
I-CAR Just In Time: Lineman’s Glove Testing
Tuesday, 7 May 2024
Sometimes seeing is understanding, that’s why I-CAR's technical team created the Just in Time video series to guide you through a variety of collision repair topics from ADAS and EVs to repair tips...
-
OEM Emergency Response Guides: BMW/Mini
Thursday, 2 May 2024
Are you looking for OEM emergency response guides (ERGs)? The Repairability Technical Support (RTS) team has located these guides and either houses them on the RTS website, provides links to...
-
I-CAR Ford Mach-E Collision Repair And Electromechanical Repair Courses
Wednesday, 1 May 2024
I-CAR has developed courses for the Ford Mustang Mach-E, a general collision repair overview and a course that covers electromechanical repair.
-
I-CAR Repairers Realm: Controlling Static During Refinishing - Now Available
Tuesday, 30 April 2024
I-CAR had a discussion on controlling static during refinishing.
-
Film Thickness Gauge For Plastic Parts - Is It Worth The Investment?
Friday, 26 April 2024
Film thickness gauges continue to be a valuable tool in the collision industry. Most shops have gauges that work with both ferrous and non-ferrous substrates. So, should shops invest in a film...
-
Body Shop Business: EV Intake Process
Wednesday, 24 April 2024
Body Shop Business has released an article highlighting the importance of the electric vehicle (EV) intake process.
-
Repairer Driven News: Matte Clearcoat Challenges
Monday, 22 April 2024
Repairer Driven News (RDN) has released an article highlighting the challenges of matte and semi-gloss clearcoat.
-
I-CAR Just In Time: EV Repair Tips
Wednesday, 17 April 2024
Sometimes seeing is understanding, that’s why I-CAR's technical team created the Just in Time video series to guide you through a variety of collision repair topics from ADAS and EVs to repair tips...
-
I-CAR RTS App
Monday, 15 April 2024
Looking for another tool for your toolbox? An informational guide at your fingertips? Well, the I-CAR Repairability Technical Support (RTS) app is what you are looking for!
- 2024
- May 2024 (4)
- April 2024 (12)
- March 2024 (12)
- February 2024 (12)
- January 2024 (10)
- 2023
- December 2023 (8)
- November 2023 (13)
- October 2023 (11)
- September 2023 (11)
- August 2023 (12)
- July 2023 (9)
- June 2023 (12)
- May 2023 (12)
- April 2023 (11)
- March 2023 (12)
- February 2023 (10)
- January 2023 (11)
- 2022
- December 2022 (11)
- November 2022 (12)
- October 2022 (11)
- September 2022 (13)
- August 2022 (11)
- July 2022 (10)
- June 2022 (13)
- May 2022 (11)
- April 2022 (12)
- March 2022 (10)
- February 2022 (11)
- January 2022 (13)
- 2021
- December 2021 (13)
- November 2021 (12)
- October 2021 (13)
- September 2021 (15)
- August 2021 (12)
- July 2021 (15)
- June 2021 (17)
- May 2021 (14)
- April 2021 (14)
- March 2021 (21)
- February 2021 (15)
- January 2021 (14)
- 2020
- December 2020 (13)
- November 2020 (17)
- October 2020 (12)
- September 2020 (14)
- August 2020 (11)
- July 2020 (18)
- June 2020 (16)
- May 2020 (14)
- April 2020 (20)
- March 2020 (12)
- February 2020 (14)
- January 2020 (14)
- 2019
- December 2019 (13)
- November 2019 (19)
- October 2019 (25)
- September 2019 (20)
- August 2019 (22)
- July 2019 (23)
- June 2019 (21)
- May 2019 (19)
- April 2019 (20)
- March 2019 (21)
- February 2019 (21)
- January 2019 (18)
- 2018
- December 2018 (19)
- November 2018 (19)
- October 2018 (17)
- September 2018 (16)
- August 2018 (21)
- July 2018 (20)
- June 2018 (21)
- May 2018 (17)
- April 2018 (19)
- March 2018 (22)
- February 2018 (16)
- January 2018 (20)
- 2017
- December 2017 (13)
- November 2017 (15)
- October 2017 (19)
- September 2017 (20)
- August 2017 (20)
- July 2017 (18)
- June 2017 (23)
- May 2017 (20)
- April 2017 (14)
- March 2017 (18)
- February 2017 (11)
- January 2017 (13)
- 2016
- December 2016 (9)
- November 2016 (14)
- October 2016 (21)
- September 2016 (11)
- August 2016 (11)
- July 2016 (8)
- June 2016 (13)
- May 2016 (10)
- April 2016 (11)
- March 2016 (12)
- February 2016 (11)
- January 2016 (8)
- 2015
- December 2015 (9)
- November 2015 (8)
- October 2015 (9)
- September 2015 (7)
- August 2015 (11)
- July 2015 (10)
- June 2015 (8)
- May 2015 (8)
- April 2015 (9)
- March 2015 (8)
- February 2015 (9)
- January 2015 (10)
- 2014
- December 2014 (12)
- November 2014 (7)
- October 2014 (11)
- September 2014 (10)
- August 2014 (9)
- July 2014 (12)
- June 2014 (9)
- May 2014 (14)
- April 2014 (9)
- March 2014 (6)
- February 2014 (1)
- January 2014 (27)