Revised I-CAR Training and Certification: Steel GMA Welding Course
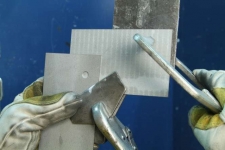
The challenges for vehicle makers to make vehicles safe and strong as well as lightweight have resulted in material variations. Many of today's steel-structured vehicles use steel in the range of 0.70 mm thickness for the outer panels, and a thicker, and in many cases higher strength, steel for the structure. This has resulted in I-CAR revising its Training and Certification: Steel GMA Welding to more accurately reflect the thicknesses of steels being used.
The revised test was released on July 30, 2012. It features ten welds made on steel coupons in two thicknesses aimed at representing steel thicknesses on today's vehicles (see Figure 1).
Based on a survey of some of the top-selling vehicles in North America, the two thicknesses selected are 22 gauge and 16 gauge zinc-coated steel. 22 gauge coated steel varies in thickness between 0.68 – 0.81 mm. 16 gauge zinc-coated steel varies in thickness between 1.4 – 1.6 mm. The original test coupons were a single thickness, 18 gauge steel. The two thicknesses selected not only represent the steel thicknesses found on current vehicles, but we feel the revised test requires a broader range of technician welding ability and verifies that the technician has the skills required to weld advanced structures.
We were especially motivated to include thin welding coupons in the test, based on several comments from test participants that they would like to test on the steel that is representative of the thin, exterior panels found on many vehicles.
Mild Steel vs. High-Strength Steel (HSS)
With the multitude of different steels used in vehicles today, material selection and sourcing presented interesting challenges. Which steels do we use? If we select specific steel strengths that represent one vehicle or OEM, how does this compare to other steels on other vehicle makes and models? To maintain a focus on weld quality and a consistent student experience, both of the coupons used in the revised test are mild steel. We found little or no difference in welder settings when making GMA welds on mild steel compared to welding on HSS, or even steel graded as UHSS.
There's another reason we went with mild steel only, and that's because of the experiences we were having with destructive testing. A successful plug weld twist test on two mild steel coupons will invariably twist a nugget out of the base metal, or bottom coupon that does not have the punched hole. Any flaw in the plug weld, such as a skip or one spot around the hole where there's no fusion, results in a nugget twisting out of the top coupon instead.
On a plug weld where the base metal is a grade of HSS and the top coupon is mild steel, there's the opposite result. A successful plug weld twist test pulls a nugget from the top, mild steel coupon instead of the bottom coupon. It may be difficult to determine, then, whether the nugget twisted out of the top coupon because it's weaker steel or because the weld is flawed in some way.
I-CAR Plug Weld Tests
Figure 2 - This technician is making plug welds to hold an insert on a rail sectioning joint.For the I-CAR Training and Certification: Steel GMA Welding course, four of the ten required welds are plug welds. These include a "thin-to-thin" plug weld (22 gauge to 22 gauge) in the vertical position. The plug weld is made in a 6 mm hole punched out of the top coupon. This represents, for example, plug welds on a pinchweld flange joining two exterior panels, such as along a wheelhouse opening. It could also represent plug welds made into a butt joint backing piece, such as along a rocker panel.
There's also a "thick-to-thick" plug weld (16 gauge to 16 gauge) in the vertical position. The plug weld is made in an 8 mm hole punched out of the top coupon. This represents, for example, plug welds made into a butt joint with backing insert when sectioning a rail (see Figure 2).
For the destructive test on these two welds, I-CAR requires a tearout hole in the bottom, base metal coupon at least 5 mm, but no greater than 10 mm. The I-CAR Training and Certification: Steel GMA Welding gauge can be used to measure the tearout hole. A tearout hole close to the size of the plug weld itself signifies a strong plug weld, but too large of a tearout indicates too much heat.
There's also a 22 gauge to 16 gauge, or "thin-to-thick" plug weld in both the vertical and overhead positions. These represent, for example, plug welds along a vertical pinchweld joining an outer B-pillar to a thicker reinforcement.
With this example, on a vehicle the thicker steel may be HSS or stronger, as is common on B-pillar reinforcements. Again, in the I-CAR Training and Certification course, we wanted a nugget to twist out of the bottom coupon, so both coupons are mild steel.
We found in our research that the more heat applied when making the plug weld, the larger the tearout hole. Since excessive heat is something to avoid when welding grades of HSS, we require a tearout hole from the bottom, thicker coupon, but that hole should be a maximum 5 mm, rather than a minimum 5 mm like the rest of the plug welds.
Other Test Welds
Figure 3 - Fillet weld lengths are 25-38 mm. The short length allows the weld to be destructively tested easily.In addition to plug welds, there are open butt joints, butt joints with backing, and fillet, or lap welds required in the Welding Training & Certification course. All of these welds are done on the same thickness materials (see Figure 3).
There's a vertical open butt joint using two thin coupons, which represents a common joint required on pillars and rocker panels on Toyota vehicles, for example. There's an overhead butt joint with backing using three thick coupons. This represents, for example, a common joint when sectioning a front lower rail on a Chrysler vehicle. There are two thin-to-thin fillet welds required, both a vertical and overhead. These represent the joints where an exterior panel is lapped over another exterior panel.
The Test Site is Your Site
As has been the case for several years, an I-CAR instructor will administer the test at your repair facility using your own welding equipment. This helps ensure you're familiar with the equipment and surroundings. Also, the tips on maintenance and tuning the welder will give you intimate knowledge of your welding equipment. The instructor provides the test coupons and a weld positioner for making the welds in the vertical and overhead positions. A check-off form, given to the repair facility prior to the test day, ensures that the facility has the right equipment and materials for the test. As an example, a large vise is required for destructive testing of the welds (see Figure 4).
Figure 4 - A large vise is required for destructive testing.Like any I-CAR event, the Training & Certification: Steel GMA Welding is administered in a supportive and friendly learning environment. The instructor leads a practice session, as much as is required, and offers guidance throughout to help ensure all of the technicians making the welds are successful. It is a guarantee that by the end of the session, everyone participating in the event will know more about GMA welding and be a better welder.
Conclusion
The I-CAR Training & Certification: Steel GMA Welding has been revised to better represent the steel thicknesses being used by the vehicle makers. Ten welds are required to be made on 22 gauge and 16 gauge coupons, in a combination of vertical and overhead positions. An I-CAR instructor will administer the Training and Certification courses at the repair facility using the repair facility's welding equipment.
Major collision damage requires a greater level of expertise to repair, and welding is one of the most critical skills necessary in completing that repair safely. Poor welds can lead to part failure and reduced protection for the occupants in the vehicle. How well a technician performs welds, even the condition of the welding equipment, impacts not only the structural integrity of the vehicle, but safety, as well.
This article first appeared in the August 22, 2012 edition of the I-CAR Advantage Online.
Additional I-CAR Collision Repair News you may find helpful:
Related I-CAR Courses
-
Toyota/Lexus/Scion Position Statement: Pre- and Post-Repair System Scanning
Thursday, 28 July 2016
As the industry continues to ask if pre- and post-repair system scanning is necessary, Toyota/Lexus/Scion provides their answer.
-
Pre- and Post-Repair System Scanning Position Statements
Wednesday, 9 January 2019
Are you wondering if a particular OEM or organization has a published position statement on pre-repair and post-repair scanning? We have compiled a list of most of the position statements on the...
-
ADAS, Calibration, And Scanning Article Hotspot
Monday, 14 January 2019
Since advanced driver assistance systems (ADAS), scanning, and calibration first started becoming relevant, members of the collision repair industry have required as much knowledge as possible on...
-
Honda/Acura Position Statement: Pre- and Post-Repair System Scanning - UPDATE
Wednesday, 22 May 2019
Honda /Acura has updated their position statement on pre- and post-repair scanning to give more clarification on what is expected for scanning.
-
Restraints Wiring Repairs
Monday, 23 May 2016
Over the past few months, we've been sharing OEM position statements on restraints wiring repairs. Now we're bringing them all together in one place for easy reference.
-
Typical Calibration Requirements For Blind Spot Sensors
Wednesday, 19 October 2016
Technicians should be aware of what’s required to keep advanced driver assistance systems (ADAS) running safely after a collision. Whether that be aiming a camera, which can cause a system to not...
-
General Motors Position Statement: Pre- and Post-Repair System Scanning
Friday, 21 October 2016
As the industry continues to ask, are pre- and post-repair scans necessary, General Motors provides their answer.
-
Typical Calibration Requirements For Forward Radar Sensors
Wednesday, 12 October 2016
Technicians should be aware of what’s required to keep advanced driver assistance systems (ADAS) running safely after a collision. Whether that be aiming a camera, which can cause a system to not...
-
FCA/Stellantis Position Statement: Pre- and Post-Repair System Scanning
Thursday, 9 June 2016
FCA/Stellantis has released a position statement related to pre- and post-repair system scanning.
-
Quickly Identifying Outer Quarter Panels w/Rolled Hem Flanges
Monday, 5 March 2018
The I-CAR best practice article, Recycled Outer Quarter Panels w/Rolled Hem Flanges has gotten a lot of interest from the collision repair industry. It’s important to know which vehicles are...
-
I-CAR Repairers Realm: Paint Color Matching Challenges - Coming Soon
Friday, 17 May 2024
I-CAR is having a discussion on the challenges of paint color matching.
-
Honda Has Released The 2024 Prologue Body Repair News
Wednesday, 15 May 2024
Honda has released a Body Repair News bulletin for the 2024 Honda Prologue. This document provides relevant information at a glance for this new model which was co-developed with General Motors (GM).
-
Acura Has Released The New 2024 ZDX Body Repair News
Wednesday, 15 May 2024
Acura has released a Body Repair News bulletin for the 2024 Acura ZDX. This document provides relevant information at a glance for this new model which was co-developed with General Motors (GM).
-
GM Repair Insights: Spring 2024
Monday, 13 May 2024
The spring edition of General Motors (GM) Repair Insights magazine is now available.
-
OEM Linking Pin: Kia Outer Uniside Sectioning
Friday, 10 May 2024
As part of the I-CAR Repairability Technical Support (RTS) OEM linking pin activity, we are helping to connect the collision repair industry to the vehicle makers. We’ve had technical inquiries that...
-
Calibration Research Tips: Nissan/INFINITI - Bumper Cover Replaced With Sonar Sensor Holder
Thursday, 9 May 2024
While searching for information on advanced driver assistance systems (ADAS) on an OEM repair information site, you may come across unique calibration procedures or events. These events can vary by...
-
I-CAR Just In Time: Lineman’s Glove Testing
Tuesday, 7 May 2024
Sometimes seeing is understanding, that’s why I-CAR's technical team created the Just in Time video series to guide you through a variety of collision repair topics from ADAS and EVs to repair tips...
-
OEM Emergency Response Guides: BMW/Mini
Thursday, 2 May 2024
Are you looking for OEM emergency response guides (ERGs)? The Repairability Technical Support (RTS) team has located these guides and either houses them on the RTS website, provides links to...
-
I-CAR Ford Mach-E Collision Repair And Electromechanical Repair Courses
Wednesday, 1 May 2024
I-CAR has developed courses for the Ford Mustang Mach-E, a general collision repair overview and a course that covers electromechanical repair.
-
I-CAR Repairers Realm: Controlling Static During Refinishing - Now Available
Tuesday, 30 April 2024
I-CAR had a discussion on controlling static during refinishing.
- 2024
- May 2024 (9)
- April 2024 (12)
- March 2024 (12)
- February 2024 (12)
- January 2024 (10)
- 2023
- December 2023 (8)
- November 2023 (13)
- October 2023 (11)
- September 2023 (11)
- August 2023 (12)
- July 2023 (9)
- June 2023 (12)
- May 2023 (12)
- April 2023 (11)
- March 2023 (12)
- February 2023 (10)
- January 2023 (11)
- 2022
- December 2022 (11)
- November 2022 (12)
- October 2022 (11)
- September 2022 (13)
- August 2022 (11)
- July 2022 (10)
- June 2022 (13)
- May 2022 (11)
- April 2022 (12)
- March 2022 (10)
- February 2022 (11)
- January 2022 (13)
- 2021
- December 2021 (13)
- November 2021 (12)
- October 2021 (13)
- September 2021 (15)
- August 2021 (12)
- July 2021 (15)
- June 2021 (17)
- May 2021 (14)
- April 2021 (14)
- March 2021 (21)
- February 2021 (15)
- January 2021 (14)
- 2020
- December 2020 (13)
- November 2020 (17)
- October 2020 (12)
- September 2020 (14)
- August 2020 (11)
- July 2020 (18)
- June 2020 (16)
- May 2020 (14)
- April 2020 (20)
- March 2020 (12)
- February 2020 (14)
- January 2020 (14)
- 2019
- December 2019 (13)
- November 2019 (19)
- October 2019 (25)
- September 2019 (20)
- August 2019 (22)
- July 2019 (23)
- June 2019 (21)
- May 2019 (19)
- April 2019 (20)
- March 2019 (21)
- February 2019 (21)
- January 2019 (18)
- 2018
- December 2018 (19)
- November 2018 (19)
- October 2018 (17)
- September 2018 (16)
- August 2018 (21)
- July 2018 (20)
- June 2018 (21)
- May 2018 (17)
- April 2018 (19)
- March 2018 (22)
- February 2018 (16)
- January 2018 (20)
- 2017
- December 2017 (13)
- November 2017 (15)
- October 2017 (19)
- September 2017 (20)
- August 2017 (20)
- July 2017 (18)
- June 2017 (23)
- May 2017 (20)
- April 2017 (14)
- March 2017 (18)
- February 2017 (11)
- January 2017 (13)
- 2016
- December 2016 (9)
- November 2016 (14)
- October 2016 (21)
- September 2016 (11)
- August 2016 (11)
- July 2016 (8)
- June 2016 (13)
- May 2016 (10)
- April 2016 (11)
- March 2016 (12)
- February 2016 (11)
- January 2016 (8)
- 2015
- December 2015 (9)
- November 2015 (8)
- October 2015 (9)
- September 2015 (7)
- August 2015 (11)
- July 2015 (10)
- June 2015 (8)
- May 2015 (8)
- April 2015 (9)
- March 2015 (8)
- February 2015 (9)
- January 2015 (10)
- 2014
- December 2014 (12)
- November 2014 (7)
- October 2014 (11)
- September 2014 (10)
- August 2014 (9)
- July 2014 (12)
- June 2014 (9)
- May 2014 (14)
- April 2014 (9)
- March 2014 (6)
- February 2014 (1)
- January 2014 (27)