MIG Brazing What Is It, Why Should I Use It?
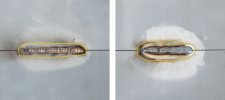
Why MIG Brazing?
It is widely known that GMA welded; fully galvanized steel will lose some of its properties, including corrosion protection, due to the heat created during welding. OEMs are starting to counter this problem by using MIG brazing along with "stitch" and "skip" methods to control the heat. However, MIG brazing should only be done in areas specified by an OEM procedure. With MIG brazing, the lower heat input burns away a minimal amount of the zinc corrosion protection (galvanizing) adjacent to the weld (see Figure 1).
Generally the melting temperature of GMA welding electrode wire is higher than the evaporation temperature of zinc 910°C (1,670°F), causing the zinc to vaporize both in and around the weld zone. However, by reducing the welding temperature, less zinc will vaporize adjacent to the weld bead and the zinc disturbed by the process will "return."
In addition to protecting the galvanized coating, the low heat involved in MIG brazing does not compromise the strength of the steel. A number of other characteristics associated with MIG brazing include:
- Less welding spatter. The material is transferred into the weld pool without any short-circuiting. As a result, the arc is almost entirely free of spatter.
- Easier finishing of the welded joint. The bronze bead is soft.
- Less potential of panel warpage when the weld heat is lowered.
- Reduced potential for burnthrough.
- A good seal along the joint. Cathodic corrosion protection next to the weld bead (cathodic corrosion protection prevents rust "creep" between zinc and steel along cut edges of the panel).
Adhesion vs. Fusion
During GMA welding, the base metal melts and fuses with the melted filler metal at a temperature of approximately 1,650°C (3,000°F). This is considered a fusion process. When brazing, however, the temperature is considerably less, with a welding temperature 1,940°F. Therefore, only the filler metal melts. It does not melt the surrounding metal in the weld zone, rather it lies on top without penetrating the base metal.
Equipment RecommendationsSome machines will automatically adjust the weld settings depending on the material thickness that is entered.MIG brazing can be performed using a GMA welding machine, equipped with a spool gun, a conventional torch, or a push feeder with Teflon cable liner. This type of liner is used to minimize particle throw-off from the filler material. Pulse MIG brazing equipment has yielded the best results when MIG brazing. Pulse equipment provides lower heat input into the base metal (see Figure 2). It uses one molten drop of electrode per pulse, which results in virtually spatter-free welding. Generally, this type of equipment has a computerized program that controls a number of different parameters and uses a conventional torch with a push feeder.
Recommended Filler Materials
The recommended brazing wire includes copper-silicon (CuSi3), which is most common for sheet steel, or bronze alloy solder (CuAl8 and CuSn6). It is recommended to treat this wire similar to aluminum wire. There cannot be any abrasions to the wire when it is fed. Therefore, use half-round, smooth wire drive rolls. Recommended base wire liners may include Teflon, plastic-graphite, or carbon fiber. The recommended shielding gas is 100% argon.
Machine Settings
The most common error that technicians make when setting a GMA welder for MIG brazing operations is setting the output of the welding machine too high and making too hot of a weld. When MIG brazing using a GMA welding machine, use a lower wire speed (lower current) setting than what is generally used for welding with steel electrode wire. Also, use lower voltage settings (shorter arc length). This requires the power source on the welder to deliver a stable arc in the low power range.
This is an example of good weld.
When welding with lower heat, the weld bead does not lay down flat. Unlike welding steel, this is acceptable. Do not adjust the heat settings to get a smoother, flatter bead. Increased heat settings defeat the benefits of lower heat MIG brazing.
Testing
MIG brazing welds may be tested in a manner similar to GMA welds. A proper weld will cause the top plate to tear out along the weld bead.
Additional I-CAR Collision Repair News you may find helpful:
MIG Brazing: What, Where, When, And Why?
Welding And MIG Brazing Hotspot
Related I-CAR Courses
-
Toyota/Lexus/Scion Position Statement: Pre- and Post-Repair System Scanning
Thursday, 28 July 2016
As the industry continues to ask if pre- and post-repair system scanning is necessary, Toyota/Lexus/Scion provides their answer.
-
Pre- and Post-Repair System Scanning Position Statements
Wednesday, 9 January 2019
Are you wondering if a particular OEM or organization has a published position statement on pre-repair and post-repair scanning? We have compiled a list of most of the position statements on the...
-
ADAS, Calibration, And Scanning Article Hotspot
Monday, 14 January 2019
Since advanced driver assistance systems (ADAS), scanning, and calibration first started becoming relevant, members of the collision repair industry have required as much knowledge as possible on...
-
Honda/Acura Position Statement: Pre- and Post-Repair System Scanning - UPDATE
Wednesday, 22 May 2019
Honda /Acura have updated their position statement on pre- and post-repair scanning to give more clarification on what is expected for scanning.
-
Restraints Wiring Repairs
Monday, 23 May 2016
Over the past few months, we've been sharing OEM position statements on restraints wiring repairs. Now we're bringing them all together in one place for easy reference.
-
Typical Calibration Requirements For Blind Spot Sensors
Wednesday, 19 October 2016
Technicians should be aware of what’s required to keep advanced driver assistance systems (ADAS) running safely after a collision. Whether that be aiming a camera, which can cause a system to not...
-
Typical Calibration Requirements For Forward Radar Sensors
Wednesday, 12 October 2016
Technicians should be aware of what’s required to keep advanced driver assistance systems (ADAS) running safely after a collision. Whether that be aiming a camera, which can cause a system to not...
-
General Motors Position Statement: Pre- and Post-Repair System Scanning
Friday, 21 October 2016
As the industry continues to ask, are pre- and post-repair scans necessary, General Motors provides their answer.
-
FCA/Stellantis Position Statement: Pre- and Post-Repair System Scanning
Thursday, 9 June 2016
FCA/Stellantis has released a position statement related to pre- and post-repair system scanning.
-
Quickly Identifying Outer Quarter Panels w/Rolled Hem Flanges
Monday, 5 March 2018
The I-CAR best practice article, Recycled Outer Quarter Panels w/Rolled Hem Flanges has gotten a lot of interest from the collision repair industry. It’s important to know which vehicles are...
-
Film Thickness Gauge For Plastic Parts - Is It Worth The Investment?
Friday, 26 April 2024
Film thickness gauges continue to be a valuable tool in the collision industry. Most shops have gauges that work with both ferrous and non-ferrous substrates. So, should shops invest in a film...
-
Body Shop Business: EV Intake Process
Wednesday, 24 April 2024
Body Shop Business has released an article highlighting the importance of the electric vehicle (EV) intake process.
-
Repairer Driven News: Matte Clearcoat Challenges
Monday, 22 April 2024
Repairer Driven News (RDN) has released an article highlighting the challenges of matte and semi-gloss clearcoat.
-
I-CAR Just In Time: EV Repair Tips
Wednesday, 17 April 2024
Sometimes seeing is understanding, that’s why I-CAR's technical team created the Just in Time video series to guide you through a variety of collision repair topics from ADAS and EVs to repair tips...
-
I-CAR RTS App
Monday, 15 April 2024
Looking for another tool for your toolbox? An informational guide at your fingertips? Well, the I-CAR Repairability Technical Support (RTS) app is what you are looking for!
-
Repairer Driven News: ADAS Radar Optimized Paint Color Resources
Friday, 12 April 2024
Changes in advanced driver assistance systems (ADAS) radar technology are introducing new refinishing considerations. Paint film thickness not only may affect the performance of ADAS radars, color...
-
Back-To-Basics: Window Tab Retractor
Thursday, 11 April 2024
Sometimes going back-to-basics can make the difference between a quality repair and a failed repair. Window regulators have evolved over the years, most now using a clip type retaining method. With...
-
High-Voltage Vehicle Paint Booth Quick Reference
Tuesday, 9 April 2024
When refinishing high-voltage (HV) vehicles, it is important to check for OEM paint booth temperature recommendations so that HV components do not get damaged in the heat.
-
Ford On Target 2024: Volume 1
Friday, 5 April 2024
Ford has released the first installment of their On Target publication for 2024.
-
3M Offers SOP And Process Hands-On Training and Skill Development
Thursday, 4 April 2024
The 3M Skills Development Center is a 15,000 sq ft facility where technicians can take a Body Repair Course or Paint Prep and Refinish Course. Both courses are majority hands-on of standard...
- 2024
- April 2024 (11)
- March 2024 (12)
- February 2024 (12)
- January 2024 (10)
- 2023
- December 2023 (8)
- November 2023 (13)
- October 2023 (11)
- September 2023 (11)
- August 2023 (12)
- July 2023 (9)
- June 2023 (12)
- May 2023 (12)
- April 2023 (11)
- March 2023 (12)
- February 2023 (10)
- January 2023 (11)
- 2022
- December 2022 (11)
- November 2022 (12)
- October 2022 (11)
- September 2022 (13)
- August 2022 (11)
- July 2022 (10)
- June 2022 (13)
- May 2022 (11)
- April 2022 (12)
- March 2022 (10)
- February 2022 (11)
- January 2022 (13)
- 2021
- December 2021 (13)
- November 2021 (12)
- October 2021 (13)
- September 2021 (15)
- August 2021 (12)
- July 2021 (15)
- June 2021 (17)
- May 2021 (14)
- April 2021 (14)
- March 2021 (21)
- February 2021 (15)
- January 2021 (14)
- 2020
- December 2020 (13)
- November 2020 (17)
- October 2020 (12)
- September 2020 (14)
- August 2020 (11)
- July 2020 (18)
- June 2020 (16)
- May 2020 (14)
- April 2020 (20)
- March 2020 (12)
- February 2020 (14)
- January 2020 (14)
- 2019
- December 2019 (13)
- November 2019 (19)
- October 2019 (25)
- September 2019 (20)
- August 2019 (22)
- July 2019 (23)
- June 2019 (21)
- May 2019 (19)
- April 2019 (20)
- March 2019 (21)
- February 2019 (21)
- January 2019 (18)
- 2018
- December 2018 (19)
- November 2018 (19)
- October 2018 (17)
- September 2018 (16)
- August 2018 (21)
- July 2018 (20)
- June 2018 (21)
- May 2018 (17)
- April 2018 (19)
- March 2018 (22)
- February 2018 (16)
- January 2018 (20)
- 2017
- December 2017 (13)
- November 2017 (15)
- October 2017 (19)
- September 2017 (20)
- August 2017 (20)
- July 2017 (18)
- June 2017 (23)
- May 2017 (20)
- April 2017 (14)
- March 2017 (18)
- February 2017 (11)
- January 2017 (13)
- 2016
- December 2016 (9)
- November 2016 (14)
- October 2016 (21)
- September 2016 (11)
- August 2016 (11)
- July 2016 (8)
- June 2016 (13)
- May 2016 (10)
- April 2016 (11)
- March 2016 (12)
- February 2016 (11)
- January 2016 (8)
- 2015
- December 2015 (9)
- November 2015 (8)
- October 2015 (9)
- September 2015 (7)
- August 2015 (11)
- July 2015 (10)
- June 2015 (8)
- May 2015 (8)
- April 2015 (9)
- March 2015 (8)
- February 2015 (9)
- January 2015 (10)
- 2014
- December 2014 (12)
- November 2014 (7)
- October 2014 (11)
- September 2014 (10)
- August 2014 (9)
- July 2014 (12)
- June 2014 (9)
- May 2014 (14)
- April 2014 (9)
- March 2014 (6)
- February 2014 (1)
- January 2014 (27)